금형도 필요없다…4개월 걸리던 시제품 20일이면 개발…글로벌 車업계 3D프린터 활용 열풍
-
기사 스크랩
-
공유
-
댓글
-
클린뷰
-
프린트
제작 비용 30~70% 절감…다품종 소량생산에 강점
람보르기니·포드 등 활발…현대차도 본격 참여 나서
람보르기니·포드 등 활발…현대차도 본격 참여 나서
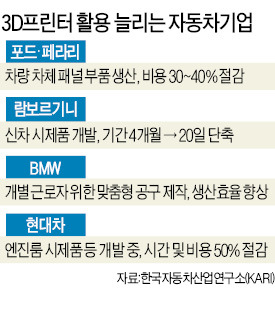
현대차그룹 한국자동차산업연구소(KARI)는 23일 ‘3D프린팅 기술이 가져올 미래 산업의 변화’ 특집 보고서를 통해 이처럼 3D프린터를 활용한 글로벌 자동차 업체들의 차량 및 부품 개발·제작이 점차 확산되고 있다고 밝혔다. 보고서는 자동차 산업에서 3D프린터 기술이 본격 상용화되면 △제조공정 단순화 △개별 주문생산 확대 △소규모 자동차 제조회사 등장 등의 파급 효과가 일어날 것이라고 분석했다.
보고서는 또 이탈리아 스포츠카 브랜드인 람보르기니가 신형 슈퍼카 ‘아벤타도르’를 개발할 때 3D프린터를 활용해 시제품 개발기간을 기존의 4개월에서 20일로 단축했다고 전했다. 페라리도 3D프린터를 차체 패널 제작 등에 제한적으로 활용하고 있다.
자동차 업체들이 아직 초보 단계이긴 하지만 3D프린터 기술을 도입하는 것은 신차 개발 등의 시간 단축과 비용 절감에 도움을 줄 것으로 기대돼서다.
곽기호 한국기계연구원 선임연구원은 “3D프린터는 별도의 금형을 만들지 않아도 설계도만 있으면 시제품을 제작할 수 있다”며 “제조 공정이 줄고 제품 수정이 쉬워 생산비용이 30~70%까지 절감된다”고 설명했다. 그는 지난해 22억달러(약 2조4000억원) 규모인 전 세계 산업용 3D프린터 시장이 2021년에는 108억달러(약 11조67000억원)로 5배가량 성장할 것으로 내다봤다.
3D프린터 기술 발전에 맞춰 자동차 산업 흐름이 소품종 대량생산에서 다품종 소량생산으로 이동할 것이라는 예상도 나온다. 이항구 산업연구원 기계전자산업팀장은 “생산비용 절감으로 개개인의 취향에 맞춘 차량 제작이 가능해진다”며 “고급 브랜드에서 이뤄지는 맞춤형 생산이 포드나 현대차와 같은 양산 브랜드로 확대될 것”이라고 설명했다.
실제 현대차도 3D프린터로 엔진룸 시제품을 만들어 개발 기간(60일→30일)과 비용(3억원→1억4000만원)을 절반으로 줄인 것으로 전해졌다.
해결해야 할 과제도 있다. 가장 큰 문제점은 생산 속도다. 3D프린터로 부피 60㎤짜리 조형물을 만드는 데 1시간이 걸린다. 기존 사출 금형을 이용한 제조 속도(1분)와는 비교가 안 된다. 전 세계 산업용 3D프린터 시장을 미국의 스트라타시스와 3D시스템즈 두 회사가 75%가량 점유하고 있는 것도 부담이다. 모세준 KARI 연구위원은 “국내에서도 3D프린터 제조와 프린팅서비스 산업 육성에 나서야 한다”며 “이와 함께 대당 5억~10억원에 달하는 산업용 3D프린터를 중소 부품업체들이 활용할 수 있도록 정부와 민간 기업이 협력해 3D프린팅 지원센터를 세울 필요가 있다”고 지적했다.
최진석 기자 iskra@hankyung.com