"공장 혁명 못하면 도태"…세계는 지금 '스마트 공장' 경쟁
-
기사 스크랩
-
공유
-
댓글
-
클린뷰
-
프린트
IoT로 제조업 환경 급변
전 단계 고객 맞춤형 제품 생산
'제조업 3.0' 시대 진입
전 단계 고객 맞춤형 제품 생산
'제조업 3.0' 시대 진입
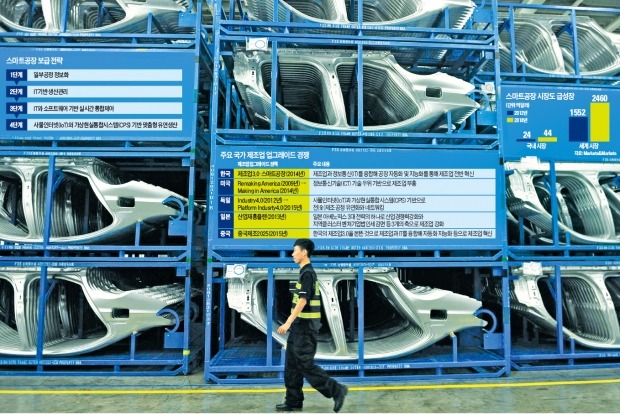
공장의 혁명은 전략이 아니라 피할 수 없는 숙제가 됐다. 똑똑한 공장을 가진 기업과 국가만이 제조업 전쟁에서 살아남을 확률이 높아졌기 때문이다.
제조업 강국들이 먼저 나서
‘공장 혁명’은 제조 공장의 수준을 업그레이드하는 과정이다. 산업혁명 이후 제조업 도입 순서대로 선진국의 순서가 매겨졌다. 2000년 전후로 제조업은 한 단계 더 도약했다. 정보화 혁명으로 가상공간에서 제품을 사고파는 환경이 조성됐다. ‘제조업 2.0’ 시대가 열린 것이다.
사물인터넷(IoT)이 출현하면서 제조업 환경은 다시 변신하기 시작했다. 물리적 공간과 가상공간이 연결된 것이다. 제조업 전 단계에서 고객 맞춤형 제품을 생산할 수 있게 됐다. ‘제조업 3.0’ 단계다.
미국이 가장 빨리 움직였다. 미국 정부는 2009년부터 ‘리메이킹 아메리카(Remaking America) 정책’을 추진했다. 세계 최고의 IT를 바탕으로 제조 방식을 첨단화하는 계획을 세웠다. 이를 위해 미국 전역에 45개 제조업 혁신연구소도 설립했다. 이 정책은 지난해 ‘메이킹 인 아메리카(Making in America) 정책’으로 이어졌다.
독일 정부는 2012년 ‘인더스트리 4.0’이라는 이름으로 공장 혁명에 뛰어들었다. 세계 일류 경쟁력을 가진 디자인, 생산, 물류 등 가치사슬을 하나로 묶어 공장 스마트화에 나섰다. 2013년에는 보쉬 지멘스 등 독일 글로벌 기업들과 함께 협력체계를 구축했다.
한국 정부도 지난해부터 ‘제조업 3.0 전략’을 추진하고 있다. 창조경제의 산업 버전에 해당한다. 중국도 자극을 받았다. ‘제조업 3.0 전략’과 비슷한 ‘중국 제조 2025 전략’을 지난 5월 발표했다. ‘중국 제조 2025’의 가장 큰 축은 공장의 스마트화다.
뒤늦게 뛰어든 한국
‘제조업 3.0 전략’을 밀어붙이는 주무 부처는 산업통상자원부다. 통상 관련 업무를 제외하면 산업부가 가장 힘을 쏟는 정책이다. 한국의 스마트공장 수준은 아직 선진국과 격차가 크다.
지난해 11월 한국생산기술연구원이 조사한 것에 따르면 한국 중소·중견기업의 스마트공장 수준은 부분 자동화를 달성한 기초 수준에 머물러 있다. 대기업도 대개 통합자동화와 지능화를 이룬 중간 수준에 그쳤다. 반면 지멘스 보쉬 테슬라 보잉 도요타 등 독일 미국 일본의 기업은 공장 혁명의 마지막 단계인 ‘완전 유연생산·가치사슬 통합’의 수준에 근접했다. 박일준 산업부 산업정책실장은 “기업과 국가의 경쟁력은 제조업 수준과 밀접한 관련이 있다”며 “한국의 공장들이 하루빨리 한 단계 더 도약하지 않으면 안 되는 이유”라고 말했다.
산업부는 지난해 스마트공장 전략을 발표하면서 매년 2000억원 이상을 투입, 올해 1200개를 시작으로 2020년까지 1만개 기업에 스마트공장을 보급하겠다고 했다. 올해 11월 말까지 기업 1240개에 스마트공장을 보급했거나 보급 중에 있다.
‘새한진공열처리’라는 회사는 산업부의 도움을 받아 1억5000만원을 들여 생산전력감시모니터링시스템(EMS)과 생산관리시스템(MES)을 설치했다. 이후 전력소비를 계측 분석해 설비 간 중첩 운전을 최소화하고 전력 피크타임 운전을 제어해 전기요금을 30% 줄였다. 불량률도 60% 감소했다. 지난 5월 대한상공회의소가 조사한 결과 스마트공장을 도입한 회사들은 평균적으로 불량률이 33% 감소했고, 원가는 23% 줄었으며 납기는 27% 짧아지는 성과를 냈다.
김재후 기자 hu@hankyung.com