G2 판매늘며 공장 풀가동…불량률 제로 달성 구슬땀
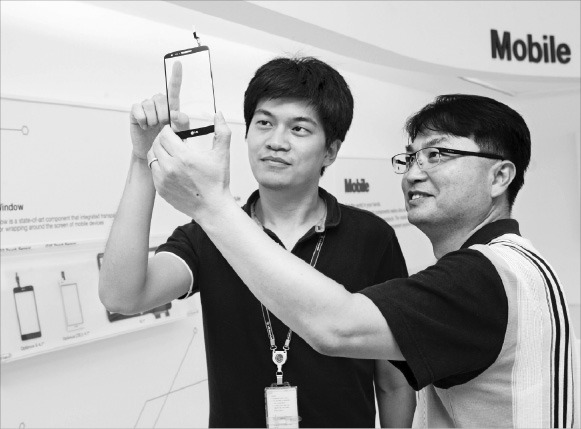
LG이노텍의 경북 구미2공장에서 터치 윈도를 생산하는 P6동 곳곳에 붙은 표어다. 이 곳에서는 LG전자가 지난달 출시한 스마트폰 G2에 적용된 터치 윈도를 생산한다. 터치 윈도는 터치 센서와 휴대폰 화면인 투명 윈도를 결합한 입력 장치다.
LG이노텍은 2008년 처음 터치 윈도 연구개발(R&D)을 시작해 지난해 8월 세계 최초로 필름 없이 글라스에 센서층을 만든 셀 타입의 커버 유리 일체형(G2) 터치 윈도 양산을 시작했다. 기존 글라스 한 개에 필름 두 장을 덧댄 필름전극방식(GFF)에 비해 두께는 얇으면서 선명도는 높다.
민감한 센서와 복잡한 회로 공정 때문에 생산라인엔 한 톨의 미세먼지도 허용되지 않는다. 무진복과 마스크, 무진화를 신고 정전기 방지를 위해 두 개의 장갑을 낀 후 에어샤워까지 마쳐야 안으로 들어갈 수 있다.
라인 한쪽 옆으로는 현상과 에칭, 박리 공정이 진행 중이었다. 0.02㎛ 두께의 센서층에 눈에 보이지 않는 수천개의 설계 회로를 새기는 정밀한 과정이다.
G2 터치 윈도는 LG전자가 지난해 9월 출시한 옵티머스G에 처음 적용됐다. 커버유리 일체형 터치 윈도의 첫 양산으로 주목을 받았지만 처음엔 제대로 된 완성품 비율인 수율이 기대에 미치지 못했다.
김종일 터치 윈도 개발팀 수석연구원은 “당시엔 매일 저녁 7시 회의를 하고 다음날 아침까지 지적사항에 대한 개선방안을 마련하기 위해 꼬박 밤을 새우기도 했다”고 전했다. 300억원 넘는 연구비를 투입한 개발과정에서 다시 수백억원의 불량품을 버려야 했다. 개발팀 소속 40여 연구원들은 3개월 넘게 밤낮없이 수율 높이기에 매달렸다. 김 수석연구원은 “고민 끝에 나온 답은 막을 입히는 증착 방식이 아닌 찍어내는 인쇄 공법이었다”고 말했다.
지난달 선보인 LG전자의 전략폰 G2엔 보다 업그레이드된 G2 터치 윈도가 적용됐다. 베젤(테두리) 공간을 차지하던 배선을 양쪽으로 나눈 듀얼 라우팅(dual routing) 공법을 새로 도입해 베젤 두께를 1.9㎜까지 줄였다. 스마트폰 측면 두께까지 포함해도 2.65㎜에 불과하다.
홍혁진 터치 윈도 생산실장은 “2㎜도 안 되는 베젤은 세계 최초”라며 “휴대폰 크기를 그대로 유지하면서 화면을 키울 수 있어 손으로 잡는 느낌이 좋다”고 말했다.
G2의 늘어나는 판매량에 대비해 요즘 공장은 완전 가동 체제다. 올 상반기 생산 규모도 기존의 두 배인 월 100만장으로 늘렸다. 회사 측은 2008년 터치스크린 사업을 시작한 후 본격적인 매출이 발생하기 시작한 2010년에 비해 올해 10배 이상의 매출 성장을 예상하고 있다.
윤정현 기자 hit@hankyung.com