이계영 현대제철 기술연구소장 "자동차·선박용 특수강 개발 집중…글로벌 경쟁력 강화"
-
기사 스크랩
-
공유
-
댓글
-
클린뷰
-
프린트
Cover Story - 현대제철
인터뷰 - 이계영 < 현대제철 기술연구소장 >
신형 제네시스에 들어간 초고장력 강판 제작
올초 터키서 교량용 후판 수주
연구원 2년내 600명으로 확대
무게 대폭 줄인 초고강도 강판 등 차세대 철강제품 개발 박차
인터뷰 - 이계영 < 현대제철 기술연구소장 >
신형 제네시스에 들어간 초고장력 강판 제작
올초 터키서 교량용 후판 수주
연구원 2년내 600명으로 확대
무게 대폭 줄인 초고강도 강판 등 차세대 철강제품 개발 박차
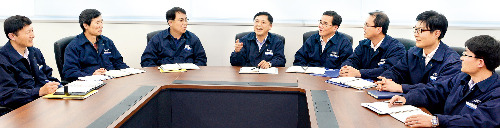
이계영 현대제철 기술연구소장은 23일 “일반 철강회사들은 자동차 엔진과 기어 등에 들어가는 소재인 특수강을 비롯해 다양한 특수소재 개발에 적극적이기 어렵다”며 이같이 말했다. 이어 “현대제철 기술연구소는 전체 연구개발(R&D) 역량의 절반가량을 자동차 소재 부문에 집중해 완성차의 경쟁력을 높이는 데 기여할 것”이라고 강조했다.
이 소장은 2005년 전기로 공정의 품질을 개선하는 업무를 담당했다. 이후 일관제철소 건설 프로젝트에 맞춰 조업기술 준비와 표준화 및 개발지원 업무를 맡았다. 철강기술 전문가인 그는 자동차강판 개발과 양산을 주도해 온 공로를 인정받아 올해부터 기술연구소장을 맡고 있다.
○자동차·선박용 제품에 ‘집중’
현대제철은 2010년 용광로(고로)를 본격 가동했다. 그러나 기술연구소가 자동차용 강판 외판재 생산을 위한 연구를 시작한 것은 이보다 2년여 전이다. 이들은 연구를 시작한 지 4년 만인 지난해 완제품 생산에 성공했다. 다른 경쟁사들이 제품 개발에 10년 이상 걸렸던 기간을 절반 이하로 단축해 업계에서 화제가 됐다.
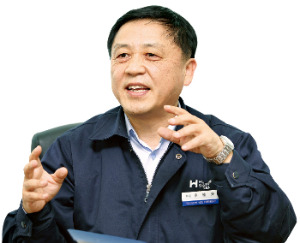
‘선택과 집중’ 전략도 주효했다. 대부분의 철강사들은 조업 초기엔 범용성이 뛰어난 저급 제품을 개발한 뒤 차츰 고급 제품으로 시장을 넓혀왔다. 하지만 현대제철은 처음부터 조선용 특수강재와 자동차용 특수강 등의 개발에 초점을 맞췄다. 이 소장은 “일관제철소 전체에서 1200만t의 쇳물을 생산하는데 이 중 자동차용 강재가 490만t에 이른다”며 “연구개발도 자동차 소재 부문에 집중하는 게 당연하다”고 전했다.
고로가 가동되기 3년 전인 2007년 2월에 문을 연 현대제철연구소는 현대차그룹 석·박사급 연구인력 430명가량이 근무하고 있다. 최근 현대하이스코에서 넘어온 70여명을 포함한 숫자다. 이들은 주기적으로 기술교류회를 갖는 등 합동 연구를 진행하며 자동차 강판을 개발했다.
연구소에 대한 아낌없는 투자도 개발 속도를 높이는 원동력이 됐다. 현대제철 기술연구소는 열간압연 모사 시험기 등 일관제철 공정을 그대로 시현할 수 있는 설비 9가지와 분석장비 136가지 등 세계 최고 수준의 시험설비를 갖추고 있다. 이 소장은 “실제 생산조건을 그대로 시뮬레이션할 수 있는 제반 설비를 갖췄기 때문에 제품 개발뿐 아니라 초기부터 조업을 안정화하고 가동률을 높일 수 있었다”고 말했다.
○초고장력 강판 등 개발 가속화
현대제철은 지난해까지 4년간 총 94종의 자동차용 강판을 개발했다. 완성차를 만들 때 사용되는 강판의 99% 이상을 자체적으로 만들 수 있게 된 것이다.
고로를 가동한 2010년 내판재와 섀시용 강판 49종을, 이듬해 외판재 13종과 고강도강 22종을 개발했다. 이어 2012년에 100~120㎏/㎟급 초고장력 강종을 포함해 10종을, 지난해엔 고강도 열연도금재와 사이드아우터용 고강도 외판재 등 13종을 만들어 자동차의 뼈대를 이루는 강판 기술을 대부분 확보했다.
이 소장은 “고강도를 유지하면서도 가공 성형성을 한층 높인 고성형성 초고강도 외판재를 올해 나오는 신차에 적용할 계획”이라며 “앞으로도 새로운 강종을 계속 개발해 경쟁력을 높일 것”이라고 했다.
현대자동차가 작년에 출시한 신형 제네시스에 들어간 초고장력 강판도 현대제철 작품이다. 이 제품의 강도는 기존 제품보다 2~3배 이상 높다. 현대차는 신형 제네시스 개발 초기부터 차체 강도를 높이는 데 초점을 두고 초고장력 강판 비율을 51.5%까지 크게 높였다. 이 소장은 “자동차 업계에서 초고장력 강판을 쓰는 평균 비율은 그 절반인 20~30% 수준에 불과하다”고 설명했다.
현대제철이 초고장력 강판 양산을 위해 택한 방법은 ‘핫 스탬핑’이다. 이 공법은 900도 이상 고온으로 가열한 소재를 프레스 성형과 동시에 급속 냉각시켜 성형 전보다 강도가 3배 이상 높은 초고장력 강판을 만들어내는 것이다.
현대제철이 올초 수주한 터키 ‘보스포루스 제3교량’에 쓰일 후판도 자체 기술력이 집약된 제품이다. 이 교량은 보스포루스 해협을 연결하는 다리로 길이가 2143m에 달한다. 다리를 만드는 데 들어가는 4만3000t 중 3만t은 영하 50도 이하에서도 가공과 용접 성능을 유지하는 특수 고성능 제품이다. 이 제품을 만들기 위해 현대제철은 온도를 제어해 압연하는 기술(TMCP공법)을 적용했다.
이 소장은 앞으로 기술개발 방향과 관련해 “중장기적으로 강도가 매우 높으면서도 다루기 쉬운 고망간강과 알루미늄을 첨가해 무게를 대폭 줄인 초고강도 경량강판, 부식이 잘 되지 않는 아연망간도금강판 등 차세대 신개념 자동차강판을 선제적으로 개발할 것”이라고 설명했다. 또 극지방 등 극한환경에 적용할 수 있는 고강도 후판과 해양구조용 형강 개발 등도 주요 과제라고 전했다. 이 소장은 이를 위해 “연구원 수를 2016년 말까지 최대 600명으로 늘릴 예정”이라고 소개했다.
○냉연사업부 통합으로 경쟁력 향상
작년 말 현대하이스코 냉연사업부를 합병한 것은 기술연구소에도 큰 도전이다. 이 소장은 “열연과 냉연 부문에서 통합 시너지를 끌어내고, 중장기적으로 제품 기술경쟁력을 확보하기 위한 방법을 고민하고 있다”고 밝혔다.
그는 “종전에는 현대제철과 현대하이스코가 일종의 ‘판매자와 수요자’ 입장이었기 때문에 데이터 수집이나 문제 해결 과정에서 비효율적인 점이 있었다”며 “앞으로는 업무 효율성이 상당히 개선돼 신제품 개발 속도도 크게 빨라질 것”이라고 기대했다.
현대제철의 현재 고민은 철강공급 과잉 및 수요 침체다. 현대차그룹이라는 비교적 확실한 수요처를 확보하고 있는 현대제철 입장에서도 세계시장에서 살아남기 위한 전략을 짜는 일은 만만치 않다.
이 소장은 “주요 글로벌 철강사들은 모두 생존을 위한 전략을 짜는 데 온 힘을 다하고 있다”며 “국가별 보호 장벽이 높아지고 있는 것도 부담”이라고 말했다. 이 소장은 이 같은 상황에 대응하기 위해 “공정기술 표준화를 통해 최대한 원가 경쟁력을 높이고, 시장 중심의 제품을 만들어 수요처의 인정을 받는 게 시급하다”고 강조했다.
이상은 기자 selee@hankyung.com