어느 중기인 '12년 집념'…중국 BYD 전기차 뚫었다
-
기사 스크랩
-
공유
-
댓글
-
클린뷰
-
프린트
반정원 씨에스텍 사장
배터리 분리막 연구 개발…글로벌 기업 제치고 공급
10년 넘게 신기술 수천번 실험…미국·일본 기업 따돌려
"꼼꼼한 BYD 테스트 통과…글로벌 2차전지 업체될 것"
배터리 분리막 연구 개발…글로벌 기업 제치고 공급
10년 넘게 신기술 수천번 실험…미국·일본 기업 따돌려
"꼼꼼한 BYD 테스트 통과…글로벌 2차전지 업체될 것"
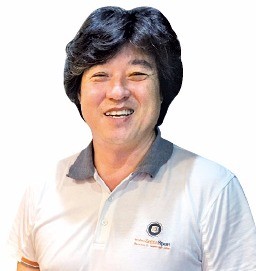
반정원 씨에스텍 사장(사진)은 23일 “BYD 전기차용 배터리에 들어가는 분리막의 50%를 공급하기로 지난달 계약했다”며 “이달 첫 물량을 보낸 뒤 공급량을 꾸준히 늘릴 계획”이라고 밝혔다. 분리막은 리튬 2차전지 내부에서 양극 물질과 음극 물질이 섞여 폭발이나 발화하는 것을 막고, 리튬 이온만 통과하게 하는 역할을 한다. 리튬 2차전지 원가의 약 17%를 차지한다.
BYD가 글로벌 기업을 제치고 씨에스텍을 분리막 최대 공급 업체로 선정한 것은 이 회사의 기술력을 높게 평가했기 때문이라는 분석이 나온다. BYD는 지난해 6만1772대의 전기차를 판매해 미국 테슬라를 제치고 글로벌 판매 1위를 기록했다. 판매량이 급증하면서 우수한 부품과 소재를 안정적으로 공급받는 게 중요해졌다.
반 사장은 “강원 원주시 공장의 생산설비를 증설해 연 2000만㎡ 수준인 분리막 생산 능력을 내년까지 5000만㎡로 늘리기로 했다”며 “BYD 납품만으로도 연 300억~400억원의 매출을 올릴 것”이라고 말했다.
씨에스텍이 셀가드 등 글로벌 기업과 중국 내 로컬 업체들을 제치고 BYD 내에서 가장 많은 분리막 물량을 확보한 이유는 간단하다. 품질 좋은 제품을 대량 양산할 수 있는 기술을 갖췄기 때문이다.
분리막은 3~4㎛(마이크로미터·100만분의 1m) 두께의 얇은 필름에 0.01~1㎛ 크기의 미세한 구멍을 뚫어 만든다. 구멍을 일정하게 많이 내면서도 내구성을 갖추는 게 핵심이다. 구멍이 손상되면 찢어지기 쉬워 무작정 많이 뚫어서도 안 된다.
씨에스텍은 제조 방식부터 기존 주요 업체들과 달랐다. 업계에서 많이 쓰는 습식이 아니라 건식을 택했다. 솔벤트 용제를 쓰지 않고 필름을 잡아 늘려 찢듯이 구멍을 내는 건식은 가격이 저렴하며 내구성이 좋고 친환경적이다. 하지만 구멍을 촘촘하고 균일하게 내기 쉽지 않다는 게 단점이었다.
반정원 사장이 처음 분리막 제조에 뛰어든 것은 2000년대 초였다. 반 사장은 “시장을 독점하던 일본 기업 등의 특허권을 피해 독자적인 분리막 제조기술을 확보하기 위해 새로운 설계를 적용하면서 숱한 시행착오를 겪었다”고 말했다.
반 사장은 압력을 가하는 방식을 두 차례로 나눠 구멍 균일도를 높이는 데 주력했다. 구멍이 일정하지 않으면 어느 한쪽으로 리튬 이온이 몰려 배터리의 안정성이 떨어지기 때문이다. 2004년 회사를 설립한 이후 6여년간 장비를 직접 설계해 제작하기를 수십 차례 반복했다. 필름에 구멍이 일정하게 뚫리는 가장 적합한 압력과 온도를 알아내기 위해 수천 번의 실험을 거쳤다.
성과는 2011년부터 나타났다. 씨에스텍 분리막을 알아본 BYD가 벤더 등록을 승인했다. 하지만 실제 물량 계약 얘기가 처음 오간 것은 2014년이다. BYD는 지난 2년 동안 신기술인 건식 분리막 제조기술의 유효성과 제품 성능 시험을 꼼꼼히 점검했다. 품질과 가격이 경쟁 기업보다 뛰어난 것이 입증되자 신규 벤더인 이 회사에 물량의 50%를 한꺼번에 몰아줬다.
반 사장은 “새로운 제조방식이어서 BYD를 납득시키고 품질을 입증하는 데 적지 않은 시간이 소요됐다”며 “BYD 외에 신규 고객사를 추가로 확보해 글로벌 2차전지 소재 업체로 성장하겠다”고 말했다.
안재광 기자 ahnjk@hankyung.com