티센크루프 천안공장, 철판 옮기고 자르고 용접하고…로봇이 13명 몫 '뚝딱'
-
기사 스크랩
-
공유
-
댓글
-
클린뷰
-
프린트
현장리포트
세계 첫 스마트팩토리 도입한 티센크루프 천안공장
직원 그대로인데 생산성 두배
3시간 걸리는 일 30분 만에
2020년 엘리베이터 국내 1위 목표
세계 첫 스마트팩토리 도입한 티센크루프 천안공장
직원 그대로인데 생산성 두배
3시간 걸리는 일 30분 만에
2020년 엘리베이터 국내 1위 목표
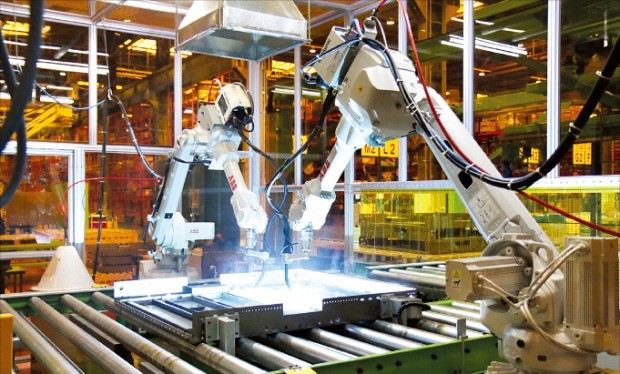
천안공장은 로봇 도입으로 시간당 생산량이 두 배 늘었다. 티센크루프 유럽 각 지사에서 “왜 한국은 직원 수가 그대로인데 생산량이 두 배 늘었냐”고 의아해하며 잇따라 방한했다고 한다. 장동윤 티센크루프엘리베이터 생산기획실장은 “작업자가 고령화되면서 산업재해 우려가 있는 위험한 일부터 로봇이 맡고 있다”며 “사람의 역할은 단순노동자에서 ‘로봇 관리자’로 변했다”고 말했다.
티센크루프엘리베이터코리아(천안공장)는 엘리베이터 업체로는 세계 최초로 ‘스마트팩토리’를 도입했다. 지난해 11월 200억원을 투자해 천안공장에 완전판금자동화설비와 로봇용접기를 도입했고 스마트물류센터도 신축했다.
티센크루프는 독일 본사가 아니라 한국 천안공장을 ‘인더스트리 4.0(독일 정부가 추진하는 제조업 혁신정책)’의 첫 번째 테스트베드로 선택했다. 장 실장은 “로봇 도입은 시작에 불과하고 사물인터넷(IoT)과 빅데이터 기술이 본격적으로 활용되면 지금까지의 생산과 판매 형태가 180도 달라질 것”이라고 강조했다.
천안공장 곳곳에는 IoT 센서가 부착돼 직원들 작업량과 시간, 품질, 사고율 등 빅데이터를 실시간으로 수집하고 있었다. 단순히 생산효율 향상만을 위한 것은 아니었다. IoT는 엘리베이터 가동 현장과 생산공장, 물류센터를 하나로 연결해 엘리베이터 사고나 부품 결함이 발생하면 생산 공정의 어느 부분과 부품에 문제가 있었는지, 고장 주기와 패턴은 무엇인지 등을 분석해 해법을 알려준다.
2020년엔 ‘가상생산시뮬레이션’도 가동돼 다양한 신제품을 사이버상에서 실험해볼 수 있다. 개발된 신제품의 설계도면을 이 시스템에 입력하면 빅데이터에 축적된 정보를 바탕으로 양산 가능 여부와 양산 기술, 효율적인 생산라인 구축 방법을 보여준다.
박양춘 티센크루프코리아 사장은 “스마트팩토리 도입이 중요한 게 아니라 이를 통해 얼마나 수익성을 높이느냐가 중요하다”며 “2020년엔 확고한 국내 1위가 목표”라고 말했다.
독일 티센크루프는 유럽에서 두번째로 큰 철강회사이자 세계 3위 엘리베이터 회사다. 천안 공장의 생산역량은 연간 2만대로 단일 규모로는 세계적인 수준이다. 연간 매출은 약 6600억원으로 이 가운데 10%는 방글라데시, 베트남, 파나마, 카타르 등 수출을 통해 벌어들였다. 엘리베이터의 ‘CPU’역할을 하는 인버터는 티센크루프내에서도 한국이 개발을 주도해 전세계에 물량을 공급하고 있다.
천안=안대규 기자 powerzanic@hankyung.com