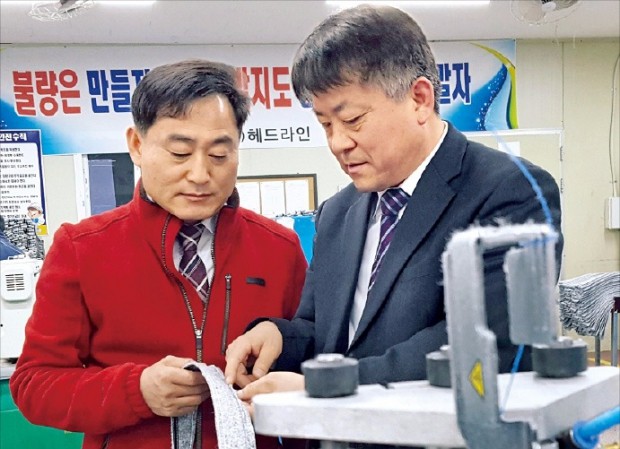

이 과정에서 삼성전자는 단순히 공정 컨설팅이나 설비 개선 지원을 넘어 스마트공장 구축까지 포함한 생산성 향상 지원에 나서고 있다. 한국생산성본부, 한국전자정보통신산업진흥회 등과 함께 제조현장을 정확히 진단한 뒤 개선이 필요한 분야와 개선 목표를 설정하고 세부 추진 계획을 수립하는 것이다. 이 과정에서 삼성전자는 개발과 제조, 구매 등에서 20년 이상 경력을 가진 임원 및 부장급 컨설턴트 100여명을 지원해 현장에 삼성전자의 경영 노하우를 전수하고 있다.
삼성전자의 산업혁신운동은 업체 수준에 맞게 단계별로 전개되는데 첫해에는 열악한 제조현장을 개선하는 데 집중 지원했다. 다음해에는 생산성 혁신을 위한 스마트공장 도입, 3년째에는 사출 및 금형 등 전문기술에 대한 지원을 강화하고 있다. 올해는 4년째로 현장의 환경안전 개선 활동까지 확대하고 있다. 지금까지 4년간 삼성전자는 1546개의 제조현장 개선과 161개사의 스마트공장 구축 지원, 60개사의 환경안전 개선 등 총 1767개사의 생산성 혁신 활동을 지원했다. 지난해까지 지원한 회사 중 949개사를 조사했더니 산업혁신운동 참여로 공정 불량률 51%, 생산성 15.6%가 향상되는 성과가 있었다.
공정불량률을 거의 없애 연 1500만원의 손실비용을 절감한 의류건조기용 패드 제조업체 헤드라인이 대표적이다. 2014년 이호준 헤드라인 대표가 산업혁신운동을 신청했을 당시 헤드라인은 어려움에 처해 있었다. 인건비가 제조원가의 상당 부분을 차지해 생산성을 개선해야 했으며 품질 관리도 잘 이뤄지지 않아 어려움을 겪었다.
헤드라인은 컨설턴트 지도하에 두 개로 분리된 공정을 한 개 라인으로 결합하는 자동화 설비를 자체 개발해 생산성을 23% 높였다. 또한 고성능 금속탐지기 구입 자금을 지원받아 연 2400만원의 불량 손실비용을 절감했다. 이를 통해 연 1500만원을 추가로 아낄 수 있었다.
노경목 기자 autonomy@hankyung.com