알파고 채용한 현대제철, '꿈의 자동차 강판' 뽑아냈다
-
기사 스크랩
-
공유
-
댓글
-
클린뷰
-
프린트
자동차 강판도 AI 설계시대
강도 40% 높인 성분조합 찾아
AI가 최적 합금 비율 계산…현대제철 "몇 달 걸리던 실험 10일로 단축"
원가상승 최소화하며 강도·가공성 40% 개선
15억개 '경우의 수'에서 최상의 성분 배합 찾아내…연구개발비 절반으로 줄여
불량강판 식별에도 활용…AI로 제조혁신 박차
강도 40% 높인 성분조합 찾아
AI가 최적 합금 비율 계산…현대제철 "몇 달 걸리던 실험 10일로 단축"
원가상승 최소화하며 강도·가공성 40% 개선
15억개 '경우의 수'에서 최상의 성분 배합 찾아내…연구개발비 절반으로 줄여
불량강판 식별에도 활용…AI로 제조혁신 박차
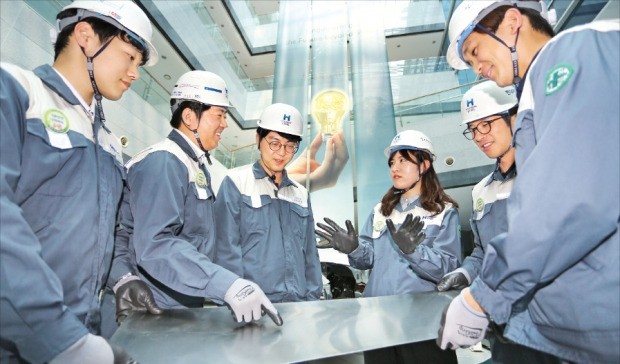
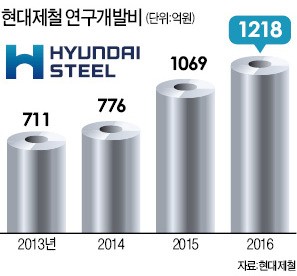
자동차 강판은 철 아연 망간 등 일곱 종의 금속 또는 합금을 배합해 제조한다. 가장 강도가 높고 가공성이 뛰어난 성분 조합을 찾아내는 것이 관건이다. 2010년 국내 한 업체는 성능을 크게 개선한 제품을 선보였다. 하지만 생산비용 증가로 너무 높게 가격을 책정하는 바람에 시장의 주목을 받지 못했다.
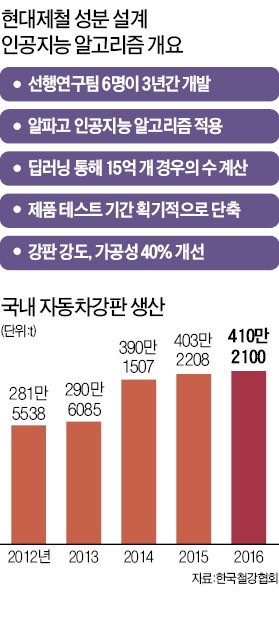
‘차세대 고유 강종 성분 설계 시스템’으로 불리는 현대제철의 알고리즘은 알파고의 방식과 같다. 알파고가 바둑을 두면서 수많은 경우의 수 가운데 최적의 한 수를 찾아내듯이 시간과 비용의 한계로 인간이 발견할 수 없었던 최적의 배합성분을 도출한다.
인간 한계를 넘어서는 R&D
알파고는 한 번의 바둑 대국에서 10의 360제곱이라는 경우의 수를 고민해야 한다. 우주 안에 존재하는 수소 원자 개수(10의 80제곱)보다 많고, 체스(10의 123제곱)보다 복잡한 과정이다. 알파고가 이세돌을 꺾을 수 있었던 것은 수천만 개의 대국을 암기해 스스로 학습한 딥러닝 기술 때문이다. 알파고는 상황마다 최선의 답을 찾는다. 이때 나오는 값은 원주율(3.14159…)처럼 딱 떨어지지 않는다. 하지만 더 이상 계산해도 같은 값이 나오는 하나의 지점으로 수렴된다. 수많은 경우의 수 가운데 알파고가 바둑돌을 내려놓는 방식이다.
현대제철 연구팀은 같은 원리를 통해 15억 개가 넘는 경우의 수에서 최적의 성분 조합을 찾아냈다. 소재, AI 분야 교수진과 현대제철 기술연구소 선행연구팀 6명이 3년간 연구한 끝에 일군 결실이다.
이번 연구에 동참한 손기선 세종대 나노신소재공학과 교수는 “알파고의 대국처럼 엔터테인먼트 분야가 아니라 제조업에 AI를 적용해 유의미한 결과물을 얻어냈다는 점은 세계에서 주목할 만한 시사점이 있다”며 “4차 산업혁명 시대를 맞아 AI와 제조업의 결합은 산업 현장의 모습을 크게 변화시킬 가능성이 높다”고 말했다.
완벽한 철강 성분 조합을 찾아내는 것은 업계의 오랜 숙원이었다. 고급 레스토랑들이 맛있는 음식을 만들기 위해 ‘황금 레시피’를 찾듯 업체마다 최상의 성분 배합을 발견하기 위해 수십 년간 공을 들여왔다. 하지만 15억 개가 넘는 경우의 수를 인간의 손으로 직접 실험하는 것은 사실상 불가능하다. 이 같은 현실적인 한계 탓에 철강업계에서는 표본연구를 하고 있다. 수십 년간 축적한 데이터와 연구원들의 노하우에 의존해야 하는 구조다. 일일이 사람의 손으로 실험을 하다 보니 연구기간은 길어질 수밖에 없었다.
불량 강판도 척척 찾아내
현대제철은 AI 도입으로 성분 배합에 투입하던 연구개발(R&D)비를 절반으로 줄일 수 있게 됐다. 몇 개월씩 걸리던 실험기간도 단 10일로 단축시켰다. 회사 관계자는 “공정 조건과 성분 세분화 작업을 거쳐 모든 경우를 사람의 손으로 계산하려면 이론적으로 8834년이 걸린다”며 “비용과 시간을 획기적으로 줄인 셈”이라고 했다.
개발 초기 회사 내부에서는 “인공지능이 우리 일자리를 뺏는 것 아니냐”는 반발도 있었다. 사람이 하던 일을 기계가 대체할 경우 직원들이 할 일이 사라지지 않겠느냐는 우려 탓이다. 그러나 알고리즘이 개발된 뒤 연구소 직원들의 인식은 달라졌다. 업무 효율성이 높아지면서 다른 연구에 쏟을 수 있는 시간이 늘었기 때문이다.
현대제철은 여러 분야에 AI 기술을 확대할 계획이다. 최근에는 불량 강판을 식별하는 자동 판독 시스템에도 딥러닝 알고리즘을 적용하는 데 성공했다. 지금까지는 10년 이상 경험을 쌓은 숙련된 작업자가 눈으로 금속조직을 판독해 불량품을 찾아냈다.
자동 판독 시스템은 숙련자 3명의 작업 패턴을 학습해 정확도를 99%까지 높였다. 작업자가 정상 제품과 불량품으로 구분할 때 금속조직을 하나하나 저장해 이를 학습한 결과다. 딥러닝을 통해 정확도는 점차 높아지고 있다. 사람의 손을 거칠 때보다 완벽한 작업을 해내는 셈이다.
박재원 기자 wonderful@hankyung.com