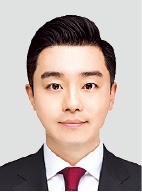
일반적인 방식으로 해당 부품을 제작하려면 재료를 많이 깎아내고 드릴로 구멍을 뚫는 과정이 필요하다. 재료 낭비가 많고 불량률이 높다는 게 단점이었다.
손 대표는 정밀 설계로 새로운 금형을 제작해 제품의 가공 공정을 최소화했다. 깎고 이어 붙이는 과정을 줄이자 제품 내구성이 향상됐다. 이 같은 넷세이프 성형기술을 활용해 재료비를 종전 대비 28% 절감할 수 있었다.
해당 공정으로 생산하는 제품 매출은 연간 20억원이 넘는다. 원가 절감과 내구성을 인정받아 현대자동차와 만도로부터 최우수 협력사로 선정됐다. 산업통상자원부의 ‘월드클래스 300 R&D 과제’ 지원을 받기도 했다.
성진포머는 이 기술 개발로 국제적인 수준의 금속 가공기술을 확보했다는 평가를 받는다. 두 건의 특허도 등록했다. 이를 바탕으로 해외 정밀금속 부품 시장에 적극 진출할 계획이다. 알루미늄과 티타늄 소재를 이용해 자동차뿐 아니라 항공부품 개발도 추진하고 있다. 손 대표는 미국 인디애나대를 졸업한 뒤 두산인프라코어 전략업무팀을 거쳐 2011년 성진포머에 입사했다.
성수영 기자 syoung@hankyung.com