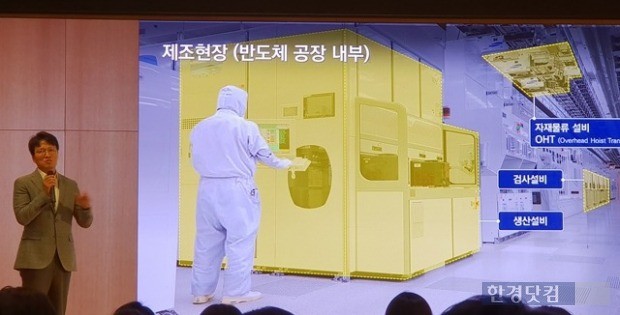
삼성SDS는 28일 서울 잠실 본사에서 미디어데이를 열어 이 같은 내용의 ‘넥스플랜트’ 플랫폼을 소개하며 외부 사업으로 확대·전파한다고 밝혔다.
넥스플랜트는 ICT로 제조업 경쟁력을 끌어올리는 데 초점을 맞췄다. 품질과 생산성 향상을 위한 삼성전자 반도체공장의 인텔리전트 팩토리를 비즈니스화했다. 제조 설비에 IoT 센서를 부착해 빅데이터를 수집, 이를 AI로 분석하며 블록체인 기술을 적용해 데이터 위·변조를 예방하는 등 첨단 ICT를 결집한 게 넥스플랜트의 특징이다.
설비 공정 검사 자재물류의 제조 4대 영역에 인텔리전트 팩토리를 구축하면 생산성을 극대화할 수 있다.
홍원표 삼성SDS 대표이사는 “제조업 경쟁이 치열해지면서 생산성을 높이기 위한 데이터 통합 관리, 최적화·지능화가 중요해졌다”며 “AI IoT 블록체인 클라우드 등 첨단 IT 기술을 활용해 기존 자동화보다 고도화된 개념인 인텔리전트 팩토리를 구현한 게 넥스플랜트”라고 소개했다.
넥스플랜트는 소음, 진동, 발열 등 실시간 이상을 감지해 장애 시점을 예측한다. 이상 원인도 자동 진단하고 복구해준다. 그 결과 설비 가동률을 높이고 생산공정을 최적화해 공정 품질을 30% 향상시킬 수 있다. 특히 AI 기반 검사 예측모델을 적용해 불량 검출률을 극대화하고 불량 유형에 대한 딥러닝(심층학습)을 통해 불량 분류정확도 역시 32% 높였다. 무인 자재물류 장치들이 공장 내를 중단 없이 최단거리로 자율주행하도록 만드는 것도 가능하다.
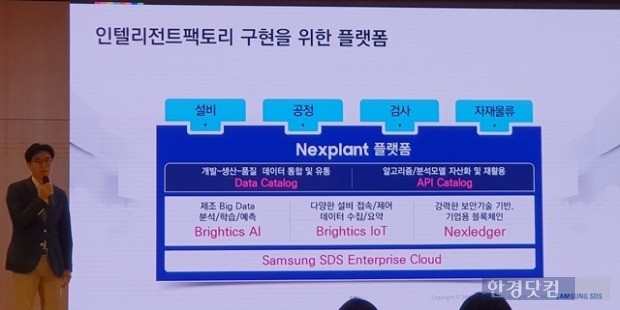
이 부장은 “한 설비에서 하루 최대 250기가바이트(GB)의 데이터가 생성되고 24시간 중단 없이 작동해 엔지니어가 일일이 관리할 수 없다. 글로벌 제조 선진회사들은 IT 신기술을 바탕으로 기존 자동화보다 한 단계 높은 지능화 단계를 완성해 경쟁력을 확보하는 추세”라고 말했다.
예를 들어 넥스플랜트를 적용하면 설비 데이터를 AI로 분석해 고장을 예측, 원인 분석 시간을 90% 단축 가능하다. 또한 통상 업계가 5% 샘플링 검사를 하는 것도 AI 기반 가상검사로 전수검사 효과를 낼 수 있다.
삼성SDS는 앞으로 넥스플랜트 플랫폼을 고도화해 플랜트 설계, 시공, 운영까지 사업을 확장해나갈 계획이다.
오세성 한경닷컴 기자 sesung@hankyung.com
기사제보 및 보도자료 open@hankyung.com