[현장+] 3년만에 찾은 LG전자 구미사업장…"주인공은 OLED TV"
-
기사 스크랩
-
공유
-
댓글
-
클린뷰
-
프린트
생산라인 줄었지만 생산량은 그대로
라인 효율화에 따른 생산성 개선 효과
플로우 방식 발전…'속도·안정성' 강화
자동화 설비 및 자동 검사 항목 확대 적용
라인 효율화에 따른 생산성 개선 효과
플로우 방식 발전…'속도·안정성' 강화
자동화 설비 및 자동 검사 항목 확대 적용
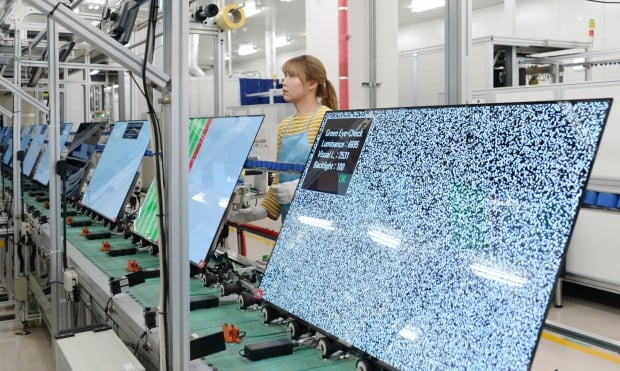
LG전자가 14일 구미사업장을 국내 언론에 공개했다. 2016년 6월 첫 공개 이후 3년 만이다. A1·A2·A3 공장으로 이뤄진 구미사업장은 가장 큰 규모인 A3 공장에서 OLED TV를 포함한 영상 제품을 생산한다. A1 공장에는 태양광 모듈 생산라인이, A2 공장은 제품 및 부품 창고로 활용되고 있다.
3년 만에 찾은 구미사업장에는 크고 작은 변화가 있었다. 모듈·메인보드·파워보드·백커버를 조립해 검사·포장하는 기본 시스템은 동일했지만, 생산의 모든 무게 중심이 OLED TV로 옮겨가 있었다. OLED TV가 그동안 얼마나 성장했는지 여실히 보여주는 부분이다.
먼저 생산라인 수가 기존 4개(G1~G4)에서 3개(G1~G3)로 줄었다. 다만 전체 생산량은 비슷하거나 오히려 늘었다. 라인 효율화에 성공했기 때문이다. 특히 모든 라인에서 OLED TV를 생산할 수 있도록 생산 방식에 변화를 줬다. 2016년에는 G3~G4 라인을 OLED TV 전용 생산라인으로 운영했는데 현재는 G1~G3 라인 모두에서 OLED TV를 생산할 수 있도록 했다.
다양한 제품 생산에 맞춰 개발된 팔레트(Pallete) 방식을 없애고 모든 라인을 플로우(Flow) 방식으로 운영했다. 컨베이어 벨트가 일정한 속도로 흘러가는 플로우 방식은 생산 속도가 빨라 효율성은 좋지만 팔레트 방식 대비 안정성이 떨어진다. 반면 팔레트 방식은 근무자가 작업 하나하나를 확인할 수 있어 프리미엄 제품 생산에 적합하지만 생산 속도가 늦다.
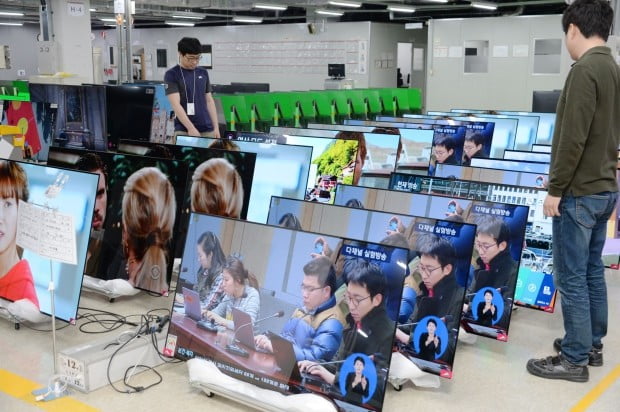
부품과 솔루션을 줄이는 모듈화 작업에 성공한 것도 OLED TV의 플로우 방식 적용 비결이다. 하나의 생산라인에서 다양한 크기·기능의 제품들을 생산할 수 있도록 LG전자는 부품과 솔루션을 결합한 모듈화 설계를 확대 적용했다. 이날 LG전자가 G3 라인에서 77인치 OLED TV와 77인치 슈퍼울트라 HD TV를 함께 생산할 수 있었던 것도 모듈화 작업 덕분이다. LG전자 관계자는 "모듈화 설계로 TV 모듈 수가 기존 100여 개에서 절반 가까이 줄었다"고 귀띔했다.
포장된 제품을 다시 뜯어 품질 테스트를 진행하는 신뢰성 검사에서도 작은 변화가 있었다. 2016년에는 모든 OLED TV를 전수 조사했지만 현재는 초프리미엄인 시그니처 OLED TV에 한해 전수 조사를 진행하고 있다. 기존 OLED TV는 일정 비율로 무작위 선택 조사하는 방식으로 바꼈다. 그만큼 생산 품질이 개선됐다는 의미다.
첫 번째 단계인 조립공정에 자동화 설비를 적용하고, 모듈을 생산라인에서 직접 조립하는 것도 과거와 달라진 모습이다. 검사의 정확도를 높이기 위해 자동 검사 항목을 늘리는 점에서도 차이가 났다.
이 같은 노력에 힘입어 LG OLED TV는 승승장구하고 있다. 2013년 4000대 수준에 불과했던 연간 출하량은 지난해 156만5000대로 늘었다. 프리미엄 입지를 강화하면서 글로벌 평가지의 호평도 계속됐다. 박근직 LG전자 HE생산담당 상무는 "철저한 품질 관리로 최상의 OLED TV를 소비자에게 제공해 왔다"며 "수요 증가. 플랫폼 변화에 대비해 LG OLED TV의 프리미엄 가치를 전달하겠다"고 다짐했다.
윤진우 한경닷컴 기자 jiinwoo@hankyung.com
기사제보 및 보도자료 open@hankyung.com