티센크루프엘리베이터코리아 충남 천안공장 가보니…스마트 공장의 힘!
-
기사 스크랩
-
공유
-
댓글
-
클린뷰
-
프린트
5년 만에 생산성 3배 뛰어
로봇이 철판 절단·용접 작업
79초 만에 승강기 도어 만들어
로봇이 철판 절단·용접 작업
79초 만에 승강기 도어 만들어
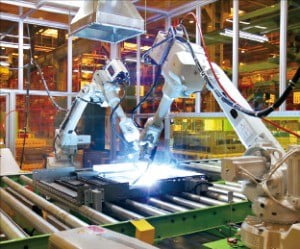
예전에는 직원 13명이 각각의 세부 공정에 투입돼 일일이 기계를 조작해 해온 작업이다. 도어 형태에 따라 20~30분까지 걸렸다. 지금은 시스템 관리에 4명만 투입될 뿐이다. 모든 공정을 기계가 한다. 윤영섭 티센크루프 스마트팩토리추진실장은 “지속적인 공장 스마트화로 생산성을 대폭 끌어올렸다”고 말했다.
티센크루프는 2012년까지만 해도 현대엘리베이터와 오티스에 이은 ‘만년 3위’ 업체였다. 2013년 점유율(한국승강기안전공단, 설치 기준) 15.8%로 오티스(13.4%)를 처음 제친 데 이어 지난해에는 24.3%까지 끌어올렸다. 2012년 4026대에 그쳤던 연간 생산 대수는 지난해 1만1570대로 뛰었다.
이 같은 성장의 원동력으로 회사 안팎에선 2012년 취임한 박양춘 사장의 리더십과 함께 공장 스마트화에 따른 생산성 향상을 꼽는다. 2016년 200억원을 들여 도입한 FMS는 대표적 스마트화 사례다. 윤 실장은 “티센크루프의 공장 스마트화는 현장에서 직접 기계를 다루는 직원들의 아이디어를 기반으로 진행한 것이 특징”이라고 설명했다.
천안공장은 곳곳에 사물인터넷(IoT) 센서를 부착해 작업량과 시간, 품질, 사고율 등 빅데이터를 실시간으로 수집한다. 불량이나 오작동이 발생하면 기계가 스스로 진단하고 바로잡는 기능도 갖췄다.
티센크루프는 설계실 직원의 제안에 따라 엘리베이터 설계도 자동화했다. 엘리베이터는 건물에 따라 디자인과 성능이 달라져야 하기 때문에 설계는 당연히 사람이 해야 한다는 고정관념을 깬 것이다. 현재는 10여 개의 특성만 입력하면 컴퓨터가 엘리베이터 도면을 알아서 설계하며, 그 도면은 자동으로 공장 내 모든 기계에 뿌려진다.
티센크루프는 재고 관리도 스마트화했다. 예전에는 어떤 재료가 어디에 들어갈지 예측하기 어려워 한 달 치씩 재고를 쌓아두기도 했으나, 현재는 빅데이터 기술을 활용해 생산 3일 전에 입고하는 시스템으로 전환했다.
티센크루프는 자동화율을 대폭 끌어올리면서도 고용 규모는 1100여 명으로 5년 전과 비슷한 수준을 유지하고 있다. 생산 공정에 투입해온 근로자들을 출하 라인 등으로 전환 배치했다.
천안=강현우 기자 hkang@hankyung.com