포스코, 철강산업에 IoT·AI·빅데이터 접목…제조업 미래 이끌 '등대공장'에 선정
-
기사 스크랩
-
공유
-
댓글
-
클린뷰
-
프린트
4차 산업혁명 이끄는 기업들
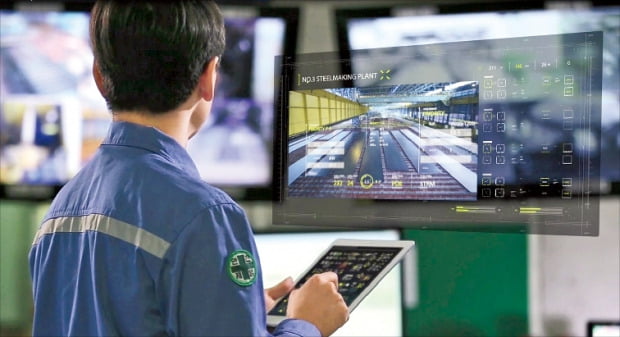
등대공장은 어두운 밤하늘에 등대가 빛을 밝혀 길을 안내하듯, 사물인터넷(IoT) 인공지능(AI) 빅데이터 등 4차 산업혁명의 핵심 기술을 적극 도입해 세계 제조업의 미래를 혁신적으로 이끌고 있는 공장을 뜻한다. 세계경제포럼은 지난해부터 세계 공장을 심사해 매년 두 차례 발표하고 있다. 세계경제포럼은 “포스코는 철강산업에서 생산성과 품질 향상을 위해 AI 기술을 적용하고, 철강산업 고유의 스마트공장 플랫폼을 구축하고 있다”고 선정 이유를 밝혔다.
포스코는 지난 50년간 축적된 현장 경험과 노하우에 IoT, AI, 빅데이터 등을 접목해 최적의 생산현장을 구현하고 있다. 포스코는 이번 등대공장 선정에 앞서 △스마트 고로 기술 △용융아연도금공장 도금량 자동제어기술 △압연 하중 자동 배분 기술 등 AI 기술 적용 사례와 현황을 세계경제포럼에 제출했다. 글로벌 컨설팅사 맥킨지&컴퍼니가 현장을 방문해 관련 기술을 검증했다.
스마트 고로는 2016년 이세돌 9단이 알파고와의 바둑 시합에서 진 이후 딥러닝에 대한 관심이 높아지면서 같은 해 하반기부터 딥러닝을 활용해 포항제철소 2고로 스마트화가 추진됐다. 딥러닝을 통해 용광로의 노황을 자동제어하는 것이다. 과거에는 용광로에 사용하는 석탄과 철광석 등을 수동으로 샘플링했다. 이제는 고화질 카메라를 설치해 석탄과 철광석의 상태를 실시간으로 데이터화해 분석하고 있다. 고화질 카메라를 통해 용광로의 연소 상태를 판단 및 예측하는 것도 가능하다. 용광로 내부의 쇳물 온도도 과거에는 사람이 직접 확인해야 했지만, 지금은 IoT 센서를 활용해 실시간으로 데이터화해 사용하고 있다.
인공지능 기반 도금량 제어자동화 솔루션은 자동차강판 생산의 핵심 기술인 용융아연도금을 AI를 통해 정밀하게 제어함으로써 도금량 편차를 획기적으로 줄일 수 있는 기술이다. 포스코는 이번에 검증된 도금량 제어자동화 솔루션을 해외 소재 법인 용융아연도금 공장에도 확대 적용해 세계 시장에서의 자동차용 도금강판 기술경쟁력을 선도하겠다는 계획이다.
제철소의 ‘핵심 근육’인 포스코 제강부는 제어가 가장 어려운 제강공정에 스마트 통합모델시스템을 적용했다. 제강공정은 고로에서 철광석을 녹여 만든 용선에 고압 산소를 전로에서 불어넣어줌으로써 탄소와 인 등 불순물을 없앤 깨끗한 용강을 만드는 과정이다. 1650도의 온도에서 조업이 이뤄져 고온과 열풍 때문에 실시간 온도 측정이 어렵고, 성분제어가 복잡해 수십 년의 경험과 노하우를 가진 취련사에게 많이 의존했다. 포항제철소 제강부는 생산제품별 대표적인 조업 경우의 수를 계산해 12만5000개의 공정을 도출한 후 빅데이터를 활용해 제강공정의 전로부터 주조까지 시간과 온도 그리고 성분을 제어하는 시스템인 PTX를 개발했다. PTX 도입 전 제강부의 제강조업 온도 적중률은 80% 수준이었으나 현재 90%로 개선됐다.
포스코는 제철소 조업 환경에 특화된 스마트 CCTV 인프라를 구축했다. 포스코가 개발한 스마트 CCTV는 제철소 현장의 특정 문자, 형상, 움직임 등을 자동으로 감지하고 이에 대한 정보를 안전, 품질, 조업 분석에 활용 가능하도록 관리자에게 알려주는 지능형 CCTV다.
고재연 기자 yeon@hankyung.com