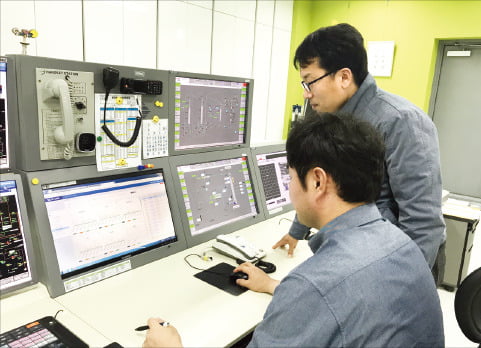
이들 자동화 시스템에 부착된 모니터링 시스템은 각 공정의 실시간 온도와 압력, 전력 사용량 등 많은 양의 데이터를 수집한다. 임직원은 이들 데이터를 통해 현재 공정이 얼마나 안정적이고 효율적으로 가동되는지 판단할 수 있다. 서울 여의도 1.5배에 달하는 대산공장엔 이 같은 모니터링 시스템이 50여 개 장착돼 있다.
현대오일뱅크는 이전에도 모니터링 시스템을 갖추고 있었다. 문제는 각 시스템이 개별적으로 설치돼 하나로 통합된 기능이 없었다는 점이었다. 자동화 시스템 제조사가 모두 달라 호환이 되지 않는 경우도 적지 않았다.
현대오일뱅크는 이 같은 문제를 해결하기 위해 2017년 8월 ‘설비통합 모니터링시스템’ 개발에 들어가 지난해 4월 새 시스템을 도입했다. 이 시스템은 현대오일뱅크가 보유한 다양한 자동화 시스템의 제조사별 특성을 감안해 가장 최적화된 방식으로 데이터 수집 및 분석이 가능하다. 공장 곳곳에 분산돼 있는 모니터링 시스템의 인터페이스 문제를 최소화할 수 있었던 비결이다. 이 시스템엔 공정의 이상 징후를 파악하고 운전원이 발생한 알람에 대응하는 데이터도 축적된다. 운전원들이 공정 현장을 방문하지 않고 사무실 내 컴퓨터 화면을 통해 설비 문제를 확인하고 필요한 조치를 할 수 있는 비결이다. 설비통합 모니터링시스템은 자주 발생하는 공정 문제 원인을 찾고 사전에 예방하는 기능도 갖췄다. 비슷한 문제 발생 시 쉽게 적용할 수 있는 지식베이스 기능을 추가한 덕분이다.
현대오일뱅크는 빅데이터 기술을 활용해 각 설비의 점검 주기와 교체 수요를 예측할 수 있도록 설비통합 모니터링 시스템을 발전시킬 계획이다.
김보형 기자 kph21c@hankyung.com