자동화 시스템으로 유연한 생산
로봇 100여대가 차체공정 100%
직원 평균 28세 '수평적 문화'
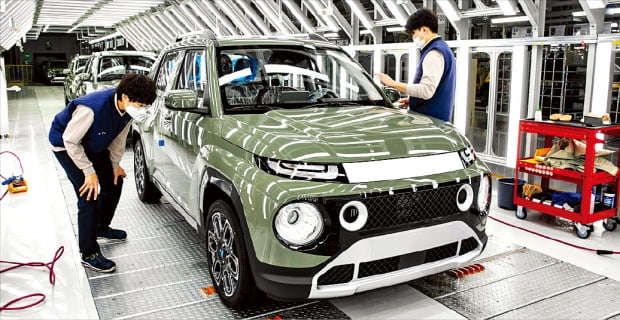
GGM의 컨베이어 벨트는 유일한 생산 차종인 캐스퍼 크기보다 훨씬 컸다. 작은 차부터 큰 차까지 다양한 차종을 생산할 수 있는 유연한 생산 체계를 갖춘 것이다. 이날 공장에서 만난 김영권 생산본부장은 “배터리, 모터 조립 공간도 생산 라인에 마련한 만큼 언제든 전기차와 수소차도 양산할 수 있는 혼류 시스템”이라고 설명했다. GGM은 친환경차 시대에 내연기관차 생산 거점으로 출발한 게 한계로 지적되기도 했다. 하지만 전기차 투입이 결정되면 바로 생산해 이 같은 우려를 불식시킬 수 있다고 회사 측은 강조했다.
GGM은 현재 연 10만 대 양산 능력을 갖췄다. 자동화율이 높아 2분18초에 한 대씩 차량을 생산할 수 있다. 차체, 도장, 조립 공장 등엔 각 100여 대의 로봇이 갖춰져 있다. 차체 공장에선 로봇이 100%, 도장 공장에선 70% 이상 공정을 담당한다. 차체→도장→조립 공장 순으로 차가 리프트를 통해 자동으로 운반된다. 공장 내 대형 모니터로는 검사 결과와 불량 대수 등을 실시간으로 확인할 수 있다.
직원들이 근무하는 조립 공장은 기름때, 먼지, 소음 등이 많은 기존 공장과는 확연히 다르게 밝고 깔끔한 분위기였다. 조립 과정에선 사소한 부분까지 안전을 고려했다. 차체를 받치는 운반대는 사람 키에 맞춰 자동으로 오르락내리락해 허리 통증을 예방해준다. 문 등 무거운 차 부품도 기존엔 사람이 지게차로 운반했지만, GGM 공장에선 자동 운반 로봇이 공정까지 실어준다. 로봇이 근무하는 작업장은 벽으로 차단돼 있다. 사람이 실수로 문을 열고 들어가면 바로 멈춘다. 박광식 GGM 부사장은 “연 20만 대까지 생산량을 늘릴 수 있도록 추가 생산라인 부지도 이미 확보해뒀다”고 말했다.
GGM 직원들의 평균 연령은 28세. 젊은 직원들은 조립공장의 컨베이어벨트에서 유니폼과 귀마개를 낀 채 분주하게 부품을 조이고 있었다. 스마트폰을 보거나 이어폰을 낀 직원은 한 명도 없었다. 약 550명이 3~5월 채용돼 400번가량 차량을 조이고 해체하는 과정을 연습했다. 전공, 자격증 등을 보지 않는 블라인드 채용으로 입사해 지금은 레벨 1~5 중 레벨 2(레벨 1이 최상위)의 조립 능력을 갖췄다. 레벨 2는 자신이 서 있는 라인에서 차량이 넘어오면 제한 시간 내 조립해 다음 공정으로 넘기는 수준을 의미한다.
광주=김형규 기자 khk@hankyung.com