13초마다 냉장고 1대 '뚝딱'…AI 무장한 LG 스마트공장
-
기사 스크랩
-
공유
-
댓글
-
클린뷰
-
프린트
'등대공장 선정' 경남 창원 LG스마트파크 가보니
생산라인을 가상 공간에 옮겨
재고 등 실시간 빅데이터 분석
현장 불량률 30%가량 줄여
600kg 상자 거뜬히 드는 로봇팔
용접·조립 등 복잡한 공정 '척척'
생산라인을 가상 공간에 옮겨
재고 등 실시간 빅데이터 분석
현장 불량률 30%가량 줄여
600kg 상자 거뜬히 드는 로봇팔
용접·조립 등 복잡한 공정 '척척'
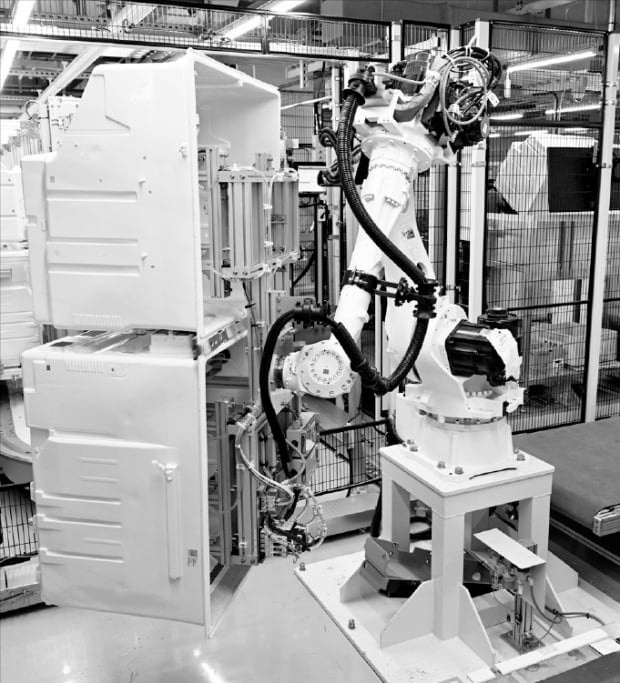
지난 6일 방문한 경남 창원시 LG 스마트파크1 통합생산동. 축구장 약 35개 규모(25만6000㎡) 공장 곳곳에 붙어 있는 표어에 눈길이 갔다. 공정 불량이나 부품 부족을 걱정할 필요가 없고, 복잡하게 얽혀 있는 거대한 생산시설 전체를 통제하고 있다는 경영진의 자신감이 느껴지는 문구였다.
디지털 트윈으로 불량률 낮춰
LG스마트파크(창원공장)는 1976년 준공돼 LG전자의 생활가전 핵심 생산거점 역할을 해왔다. 46년이나 된 공장이지만 최근 스마트팩토리로 개편하면서 세계 제조업을 이끄는 첨단 시설로 완전히 탈바꿈했다.2017년부터 스마트팩토리로 전환을 시작한 이 공장은 디지털 트윈을 비롯해 인공지능(AI), 자율주행, 빅데이터 등 첨단 디지털 전환(DX) 기술을 입혀 생산 효율은 끌어올리고 공정 불량률은 획기적으로 줄였다.
지난해 9월부터 가동을 시작했다. 지난 3월엔 국내 가전업계 최초로 세계경제포럼(WEF)으로부터 제조업의 미래를 밝히는 공장이라는 취지의 ‘등대공장’으로 선정되는 영예를 안았다.
냉장고와 오븐 등을 생산하는 LG 스마트파크1 통합생산동에선 ‘지능형 자율공장’의 면모를 곳곳에서 볼 수 있었다. 1층 로비에 들어서니 대형 화면이 보였다. 마치 게임 시뮬레이션을 하듯 화면 속에선 생산라인과 부품 이동, 재고 상황, 설비 이상 유무, 제품 생산 실적이 실시간으로 송출되고 있었다. AI와 빅데이터를 더해 분주하게 돌아가는 실제 생산라인을 가상 공간에 그대로 옮겨놓은 디지털 트윈 기술이다.
이 기술을 활용하면 자재 부족 현상 등 작업 현장에서 발생할 수 있는 이상 상태를 미리 대비할 수 있다. 30초마다 공장 안의 데이터를 수집하고 분석해 10분 뒤 라인의 상황을 예측할 수 있기 때문이다. LG전자 관계자는 “공정 문제를 선제 대응할 수 있어 라인이 멈춰서는 일을 막을 수 있다”고 말했다.
로봇 이용해 생산성 20% 개선
3층 냉장고 생산라인은 로봇과 5세대(5G) 통신 전용망을 활용한 스마트팩토리의 정수가 집약된 곳이었다. 50여 대의 자동물류로봇(AGV)이 자재를 담은 적재함을 분주하게 나르는 모습이 보였다. 실시간으로 라인별 재고를 파악하고 자재를 운반하는 AGV는 최대 600㎏ 적재함을 들어 올릴 수 있다. AGV는 바닥의 QR 코드를 인식하며 자율주행으로 정해진 목적지에 자재를 배송했다. 천장에 설치된 고공 컨베이어 레일에선 최대 30㎏ 무게의 박스가 분주하게 오갔다. 라인에선 로봇팔의 활약이 돋보였다. 로봇팔은 20㎏이 넘는 무거운 냉장고 문 조립부터 용접과 누설 검사, 나사 조이기 등 사람이 하기 어렵거나 반복적인 과정을 척척 해냈다.통합생산동은 생산라인 한 개에서 최대 58종의 모델을 함께 생산할 수 있는 혼류생산이 가능하다는 점도 특징이다. 로봇팔에 부착된 3D 카메라가 마치 사람의 눈처럼 서로 규격이 다른 제품을 확인하고 분류하기 때문이다.
LG전자는 자동화 공정 도입의 효과를 톡톡히 누리고 있다. 시간당 제품생산 대수가 20%가량 증가했다. 공장 관계자는 “약 13초마다 한 대씩 냉장고를 생산할 수 있다”고 말했다. 통합생산동에서 매일같이 수집되는 약 500GB의 데이터를 분석해 현장 불량률을 30%가량 줄였다.
LG 스마트파크는 아직 미완의 공정이다. LG전자는 현재 65% 수준인 자동화율을 2025년까지 점진적으로 높일 계획이다. 또 냉장고 생산라인 한 개를 추가하고, 오븐과 식기세척기 라인을 확대 구축할 예정이다.
창원=배성수 기자 baebae@hankyung.com