한세실업, 패션에 IT 접목…3D로 원단 폐기 최소화, 샘플 착용·포즈·사이즈에 아바타 활용
-
기사 스크랩
-
공유
-
댓글
-
클린뷰
-
프린트
독자 개발 스마트팩토리 시스템
생산 모든 과정 실시간 모니터링
워터 쿨링 장치 등 ESG도 박차
생산 모든 과정 실시간 모니터링
워터 쿨링 장치 등 ESG도 박차
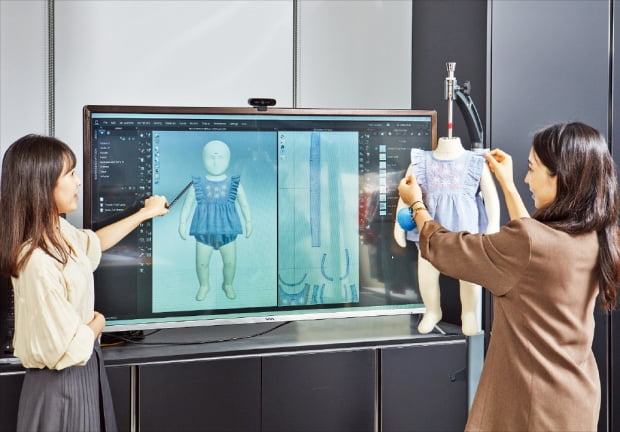
한세실업은 국내 의류 ODM업계에서 처음 버추얼 디자인(VD) 전담팀을 설립했다. 2017년부터 자체 3D(입체) 디자인 기술을 활용한 가상 샘플을 제작해 불필요한 샘플 원단의 폐기물과 포장재 및 운송 연료 등을 줄이는 데 힘쓰고 있다. 이를 통해 비용 절감과 환경 보호 효과를 모두 얻고 있다는 평가다. 한세실업 관계자는 “연구개발(R&D)센터에 대한 지속적인 투자와 전문 인력 양성을 위한 노력이 주효했다”고 설명했다.
한세 R&D센터는 코로나19로 급증한 가상 샘플링 품질 표준화 작업을 위해 3D 애셋 라이브러리 구축에 과감한 투자를 하고 있다. 패브릭의 디지털화를 위한 기술력을 강화하는 한편 원단물성 분석기를 통해 실제와 같은 원단 라이브러리를 완성했다. 비주(Vizoo)사의 표면스캐너를 도입한 기술력으로 가상 샘플링 때 실제와 동일한 원단을 구현하는 것도 기술력이다.
디자이너 전 직원이 3D 관련 자격증도 취득했다. 2025년까지 실물 샘플의 80% 이상을 3D로 대체할 계획이다. 가상 모델인 아바타 개발도 가속화하고 있다. 일반 3D 샘플 때 착용 라이선스 아바타 외 여러 다양한 포즈, 인종, 헤어스타일, 사이즈별 맞춤형 아바타 개발을 적극 추진할 계획이다.
한세실업이 독자 개발한 스마트팩토리 시스템 ‘햄스’는 생산 과정의 모든 흐름을 데이터화해 전 공장의 가동 및 생산 현황을 개인정보단말기(PAD)로 실시간 모니터링할 수 있게 돕는다. 2015년 도입된 후 고객사, 시장 상황 등 외부 변수에 따른 공장 현황을 예측하고 불필요한 업무를 덜어낼 수 있어 생산 효율을 높이는 데 기여하고 있다.
단순 반복 업무를 대신하는 컴퓨터, 알봇도 도입했다. 반복되는 질문에 자동으로 답변할 수 있는 챗봇 시스템도 사용하고 있다. 사이즈 라벨 부착, 폴리백 작업, 가먼트 폴딩 등 수작업으로 진행하던 업무 일부도 자동화해 생산 효율을 높였다.
회사 관계자는 “자동 폴딩기를 활용하면서 작업자가 기계 위에 제품을 올리면 기존 매뉴얼 작업을 자동으로 처리할 수 있다”고 말했다. 이어 “자동화 기계는 숙련도가 낮은 작업자도 고숙련자만큼 능률적으로 일할 수 있게 하고 결근에도 대응할 수 있는 게 장점”이라고 덧붙였다.
한세실업은 친환경 의류 생산 시스템 구축을 통한 ESG(환경·사회·지배구조) 경영에도 힘을 쏟고 있다. 해외 공장에는 빗물 재활용이 가능한 ‘빗물 저장 시스템’이 구축돼 있고 에어컨을 쓰지 않고 작업장 온도를 조절하는 ‘워터 쿨링 시스템’도 운영하고 있다.
고객사가 친환경 원단으로 의류를 제조하면 그로부터 발생하는 순이익의 10%를 사회에 환원하는 ‘10% 포굿(ForGood)’ 캠페인도 전개하고 있다.
김병근 기자 bk11@hankyung.com