"포스코만 만들 수 있다"…'전기 강판' 생산 광양제철소 가보니 [현장+]
-
기사 스크랩
-
공유
-
댓글
-
클린뷰
-
프린트
전기차 맞춤형 강판 '기가 스틸' 생산
'Hyper NO'로 차체 경량화·안전성 강화
"10대 중 1대 포스코 강판 사용한 셈"
자동차 강판 전문 제철소 넘어 친환경차 미래 연다
'Hyper NO'로 차체 경량화·안전성 강화
"10대 중 1대 포스코 강판 사용한 셈"
자동차 강판 전문 제철소 넘어 친환경차 미래 연다
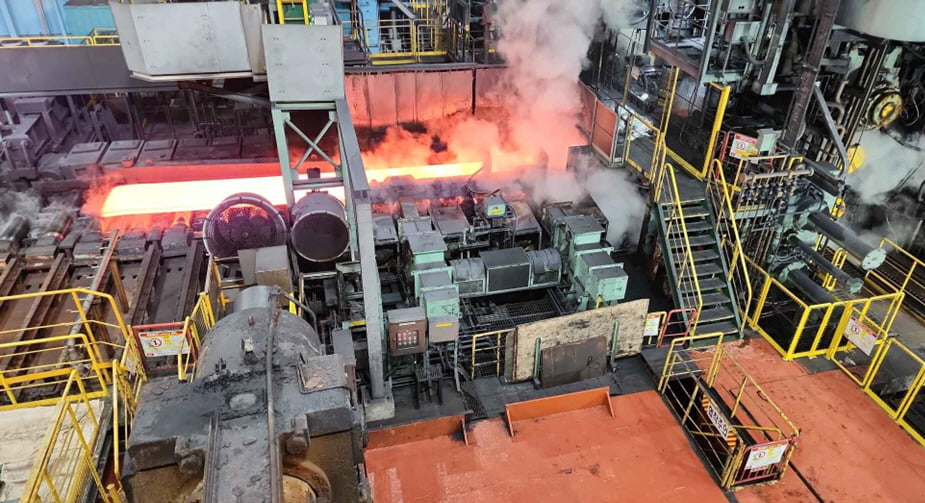
지난달 30일 방문한 포스코 광양제철소 관계자는 "하루에 일반 자동차 6만대를 만들 수 있는 양"이라며 이같이 소개했다. 전남 광양에 위치한 이곳은 자동차 강판을 전문으로 생산하는 공장이다. 면적은 여의도 7배(647만평)에 달해 단일 규모로는 세계에서 가장 크다.
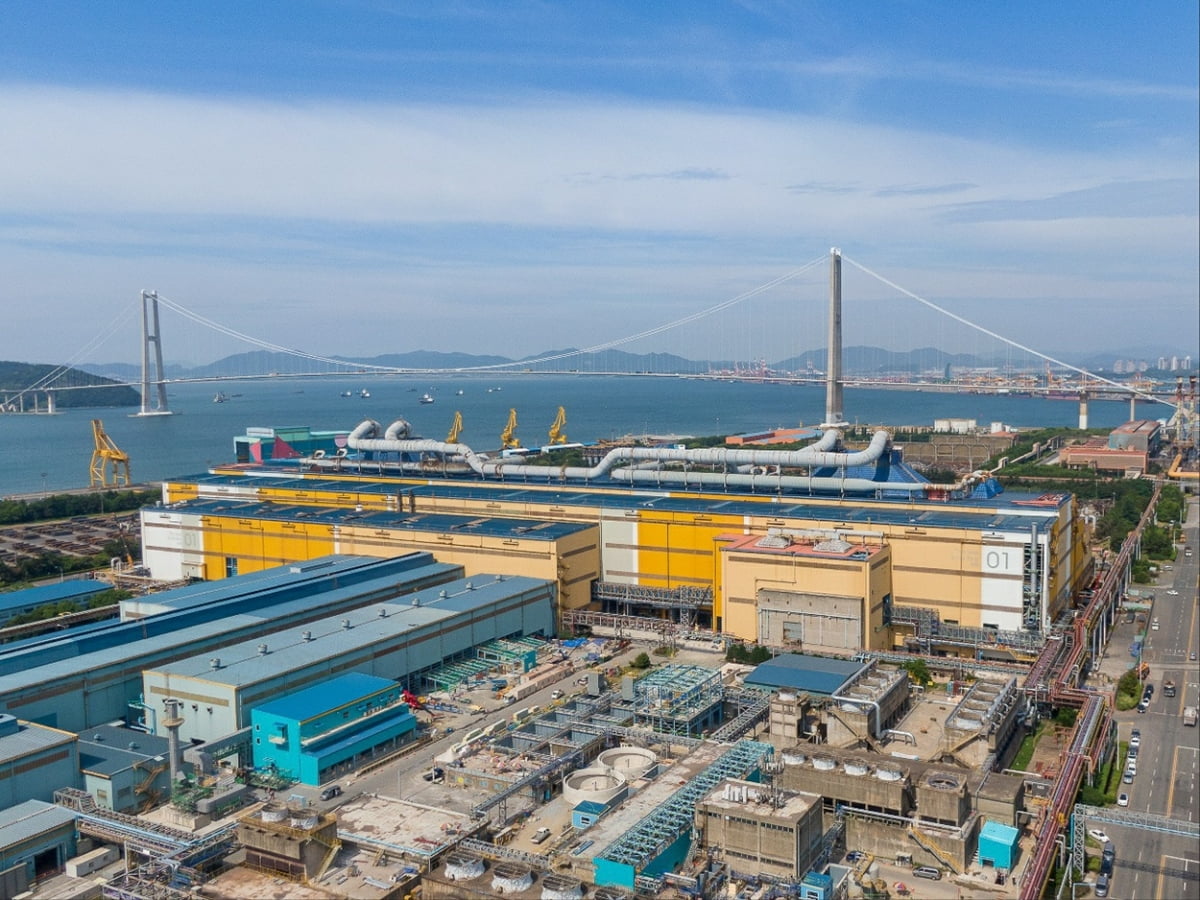
이날 방문한 곳은 철강 반제품인 슬래브를 압연해 코일로 만드는 3열연 공장과 초고강도 강판 '기가 스틸'을 생산하는 7CGL, 언론에 처음 공개된 전기 강판 공장 건설 현장이다.
!["포스코만 만들 수 있다"…'전기 강판' 생산 광양제철소 가보니 [현장+]](https://img.hankyung.com/photo/202307/06.33892842.1.jpg)
슬래브는 회전하는 롤 사이를 통과하며 얇고 길어진다. 현장 관계자는 45mm 이상 두께에서 신용카드 두께인 1.2mm까지 얇아진다고 설명했다.
!["포스코만 만들 수 있다"…'전기 강판' 생산 광양제철소 가보니 [현장+]](https://img.hankyung.com/photo/202307/06.33892847.1.jpg)
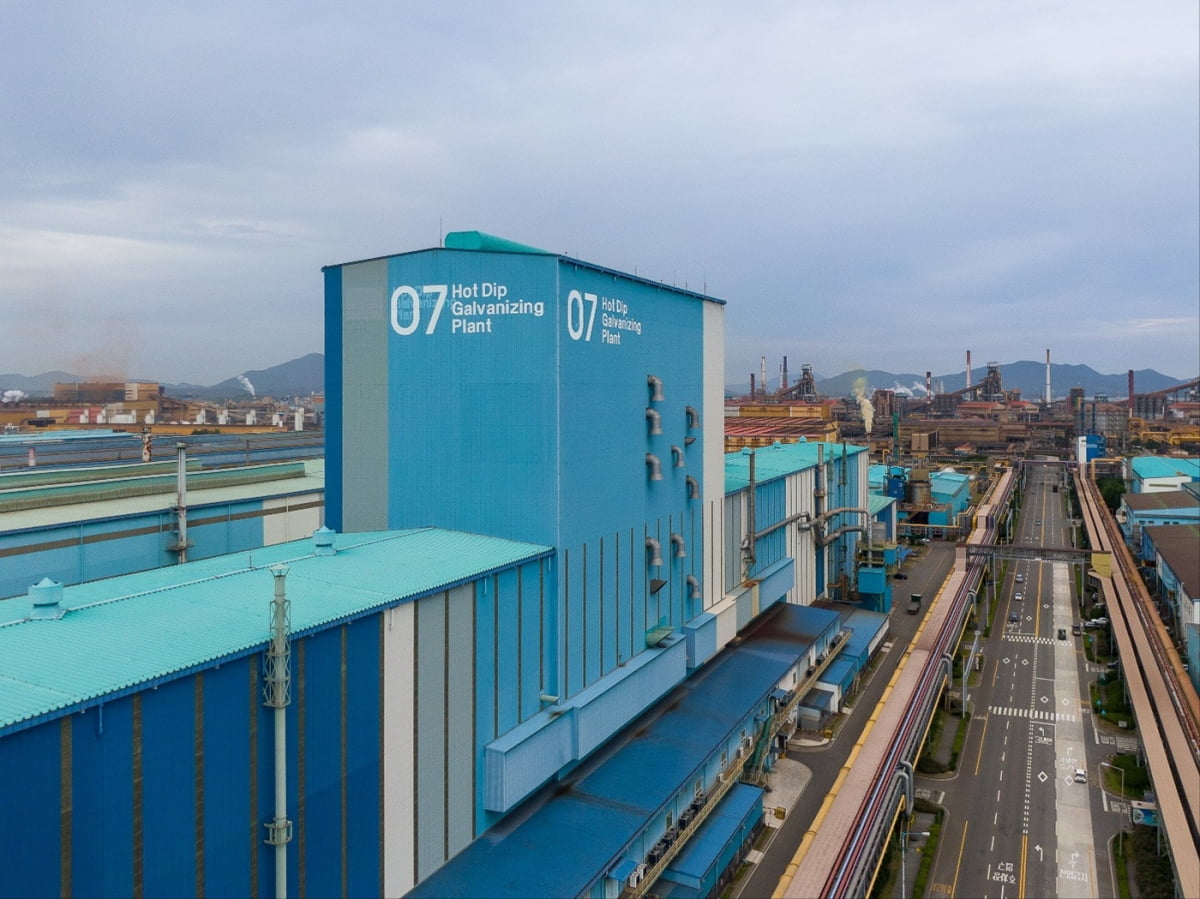
기가 스틸은 강판의 양쪽 끝을 잡아당겼을 때 늘어나는 인장 강도가 1기가 파스칼(GPa)급 강판을 뜻한다. 손바닥만 한 크기의 강판으로도 1t짜리 준중형차 1500대 하중을 견딜 수 있을 만큼 단단하다는 설명이다.
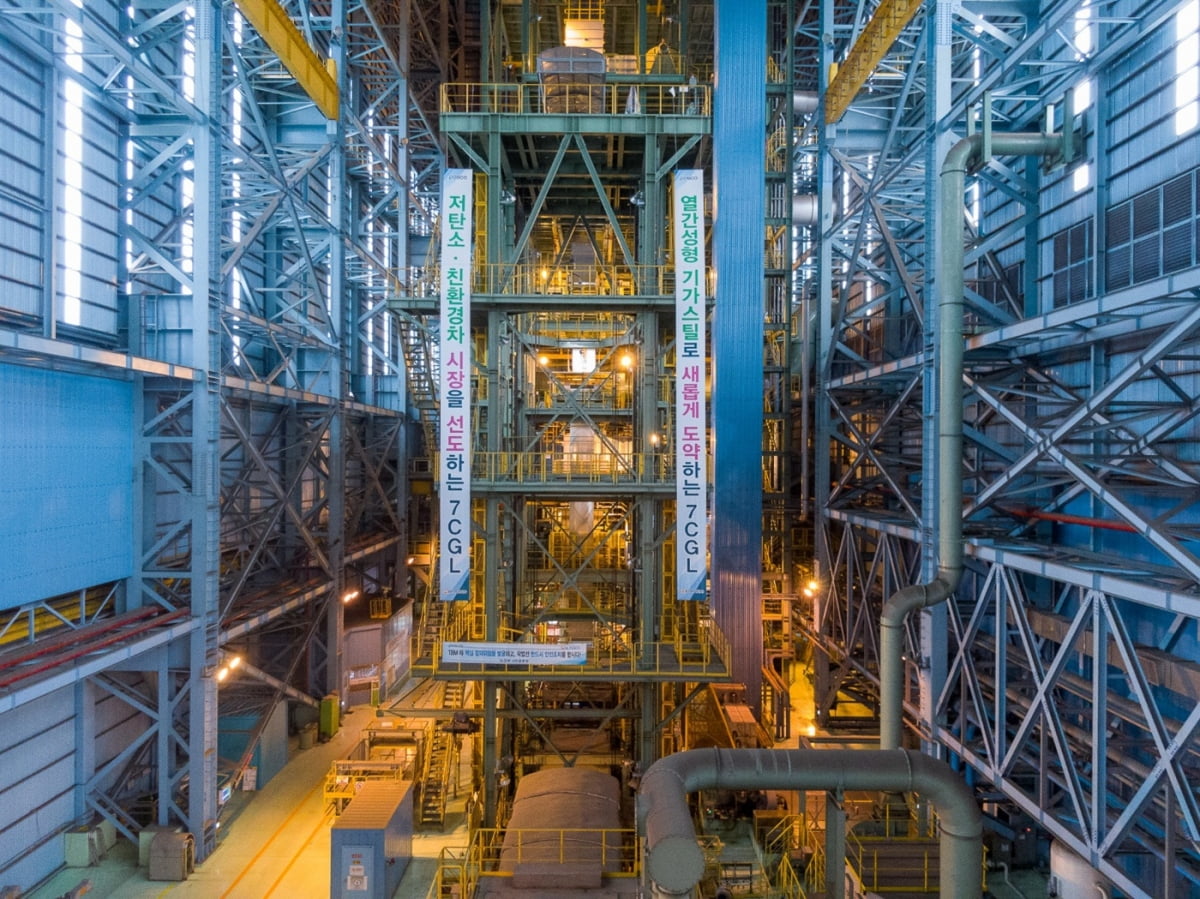
포스코는 전기차 중심으로 전환하는 자동차 산업에 대응해 기가 스틸 생산량을 늘려나가기로 했다. 또한 고강도 소재 복합 가공이 가능한 해외 가공센터를 확대하는 등 안정적 공급체계를 구축해나갈 계획이다.
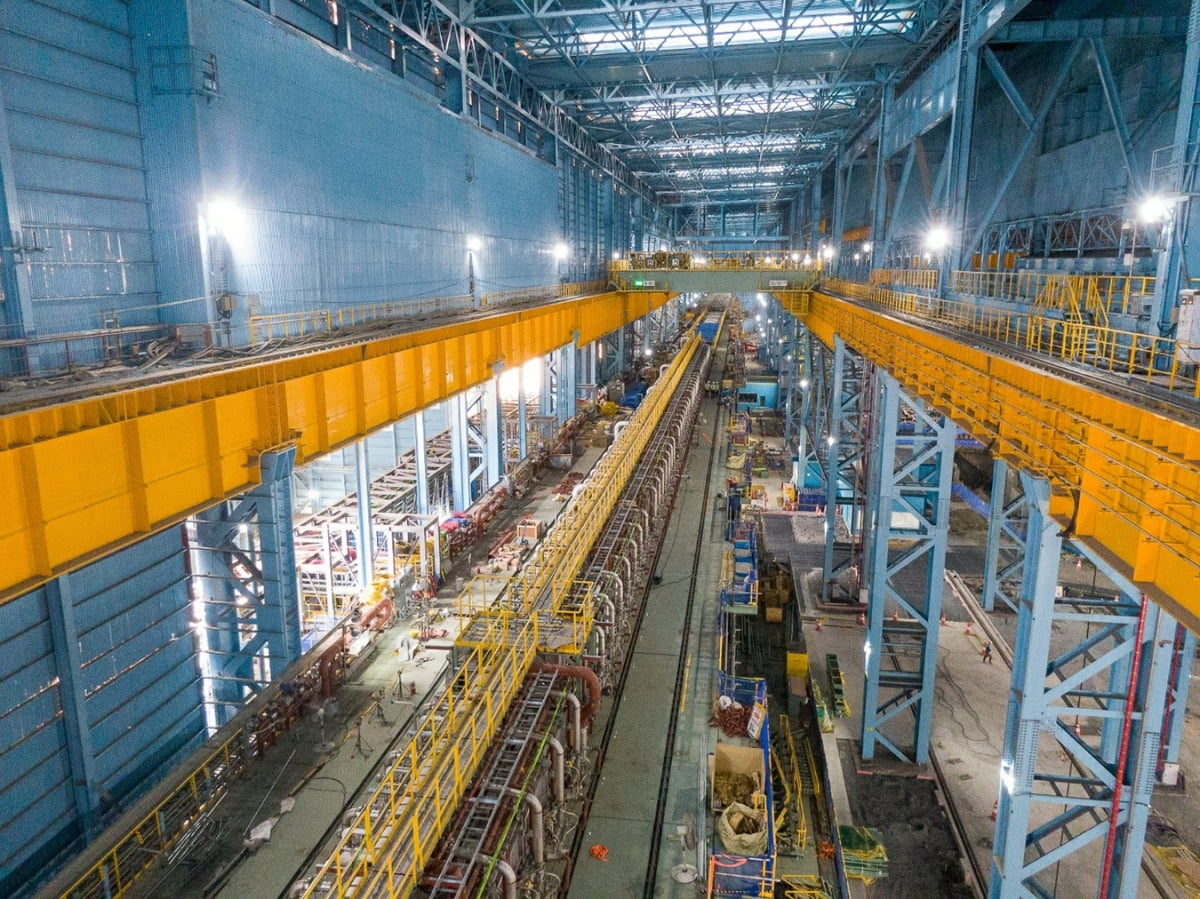
전기 강판 공장 역시 전기차의 전비를 높이는 게 핵심이다. 이곳에서는 전비에 중요한 구동모터용 무방향성 전기강판을 생산할 예정이다.
무방향성 전기 강판은 모터의 코어 철심에서 발생하는 전력 손실, 즉 철손량에 따라 등급을 나눈다. 철손값이 3.5W/kg 이하인 경우 '하이퍼 엔오(Hyper NO·고효율 무방향성 전기강판)'로 구분한다. 철손값이 낮은 하이퍼 엔오로 구동모터를 제작하면 모터 효율이 상승한다. 전기 에너지를 회전 에너지로 바꾸는 과정에서 발생하는 에너지 손실은 일반 전기 강판 대비 30% 이상 적다.
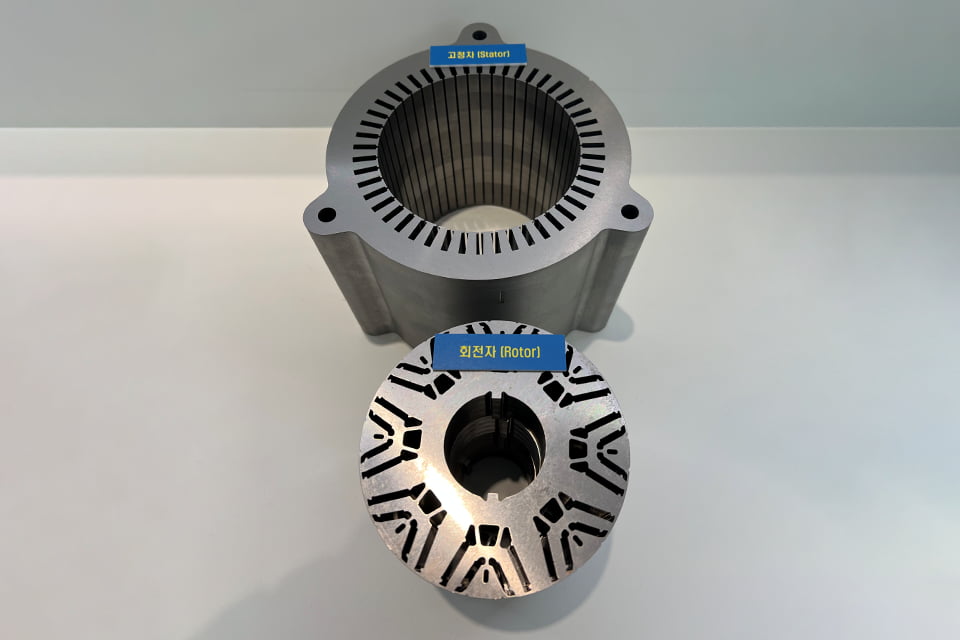
포스코가 현재 생산 가능한 하이퍼 엔오 두께는 0.15mm이다. 국내 유일의 전기 강판 생산 기술력에 최신 설비 도입으로 생산 가능 두께를 최대 0.1mm까지 낮춘다는 계획이다. 전기 강판은 두께가 얇아질수록 모터가 회전할 때 발생하는 소음과 열 등 전기 에너지 손실이 낮아져 모터의 효율이 좋아진다.
전기 강판 공장은 오는 10월 1단계 준공 예정이며 지난 3일부터 시운전을 시작했다. 내년 10월 2단계 준공이 완료되면 포항과 광양을 합쳐 연간 40만t의 하이퍼 엔오를 생산하게 된다. 전기차 500만대의 구동모터 코어를 만드는 데 쓰일 수 있는 양에 해당한다.
광양=신용현 한경닷컴 기자 yonghyun@hankyung.com