광교 갤러리아 '명품 외관' 위해…한화가 찾아낸 '이 기업'
-
기사 스크랩
-
공유
-
댓글
-
클린뷰
-
프린트
[중기탐구-숨은 1인치]
3D 프린터로 뿌리산업 인력난 극복한 삼영기계
3D 프린터로 뿌리산업 인력난 극복한 삼영기계
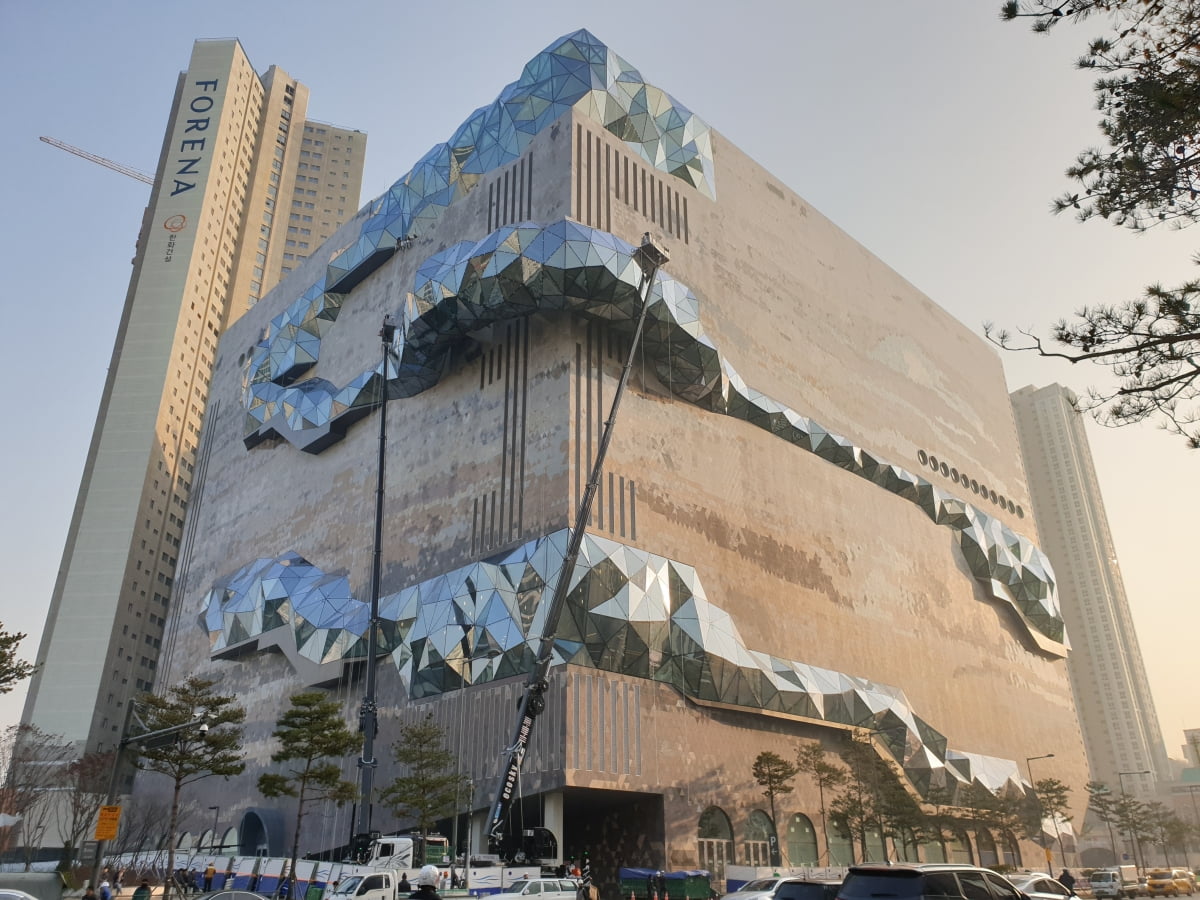
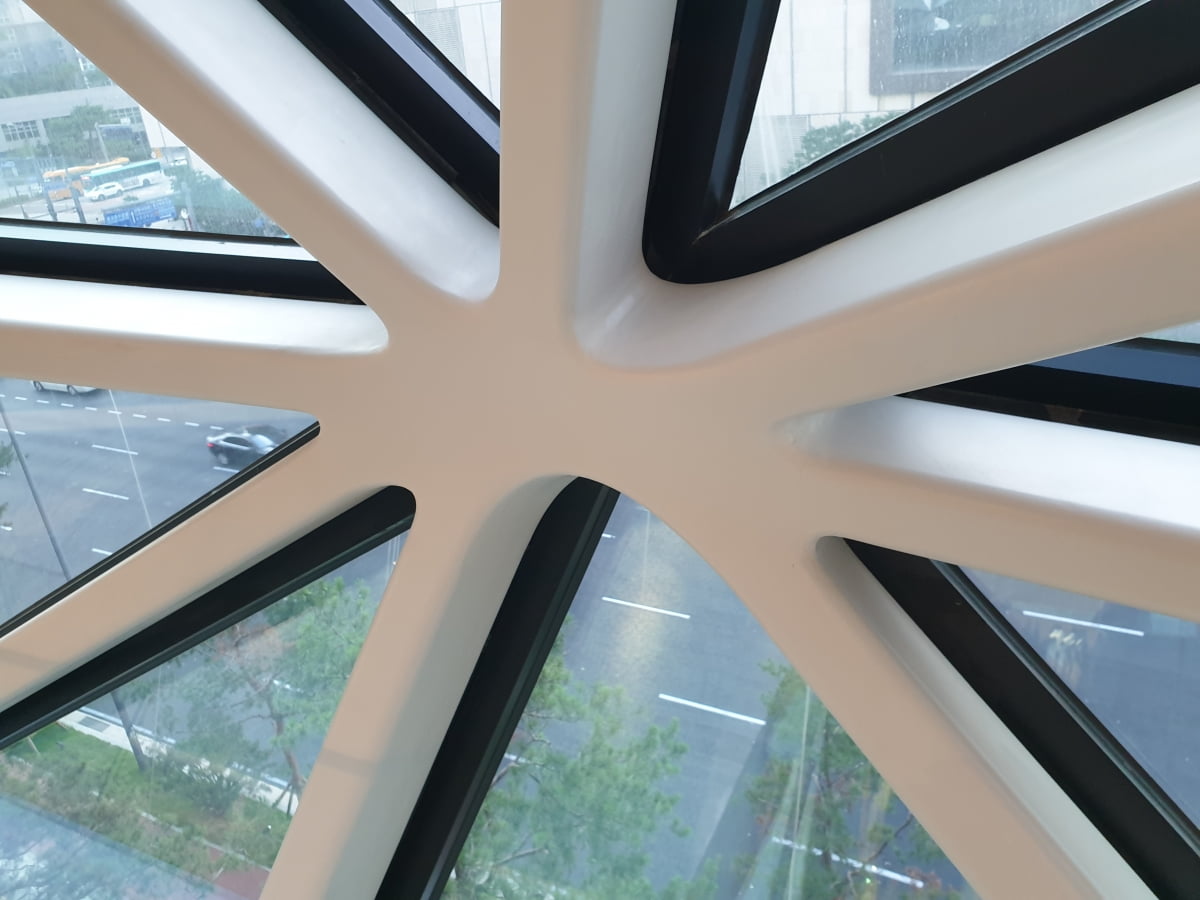
백방으로 수소문하던 한화건설이 찾은 기업이 삼영기계다. 주조 전문회사인 삼영기계는 3D 프린팅 기술로 이를 해결했다. 지난 13일 만난 한국현 삼영기계 사장은 “500개 이상의 각기 다른 형태의 노드를 전통적인 주조 방식으로 제작하려면 금속을 하나하나 깎아야 하는데 비용과 시간을 고려하면 사실상 무의미했다”며 “3D 프린팅 기술 덕에 비정형 노드를 만들 수 있었는데, 이런 모양의 건축자재를 개발한 것은 세계 최초”라고 설명했다. 건축 공법에 획기적인 변화를 가져온 광교 갤러리아백화점 파사드 시공사례는 해외 톱 저널(Journal of Building Engineering)에도 실렸다.
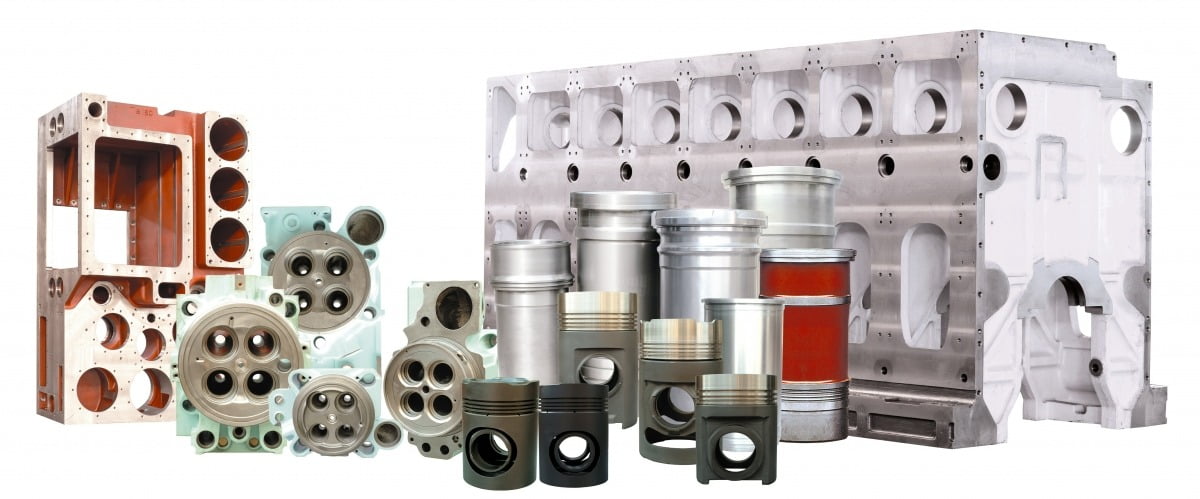
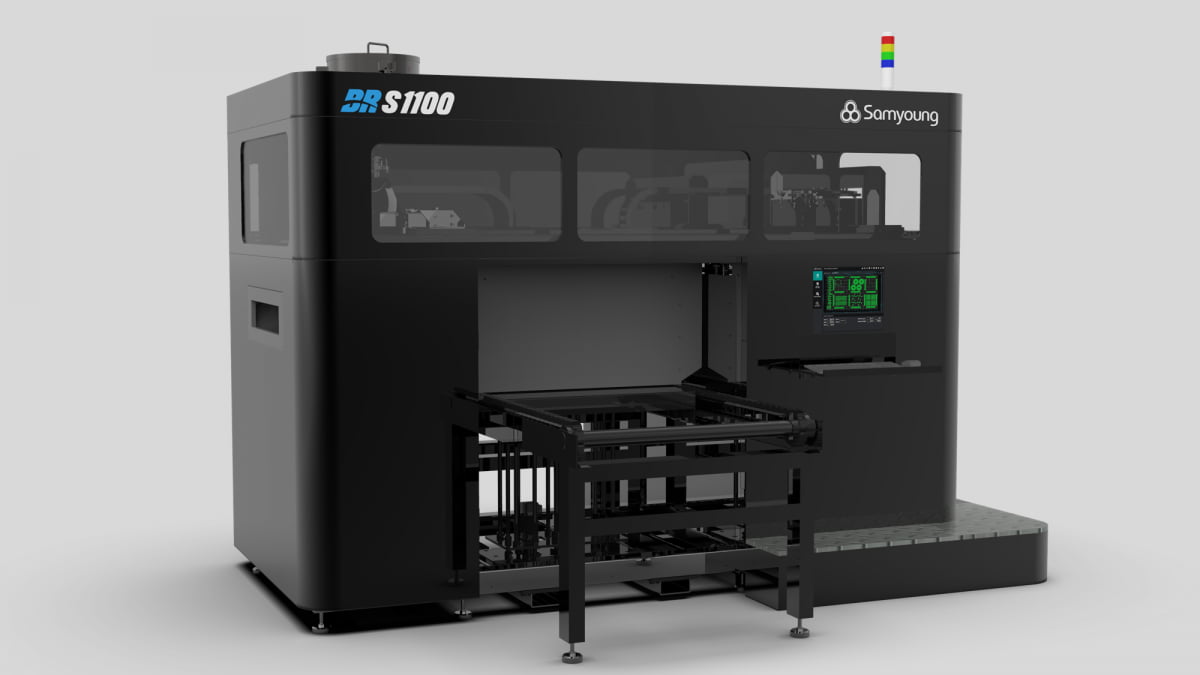
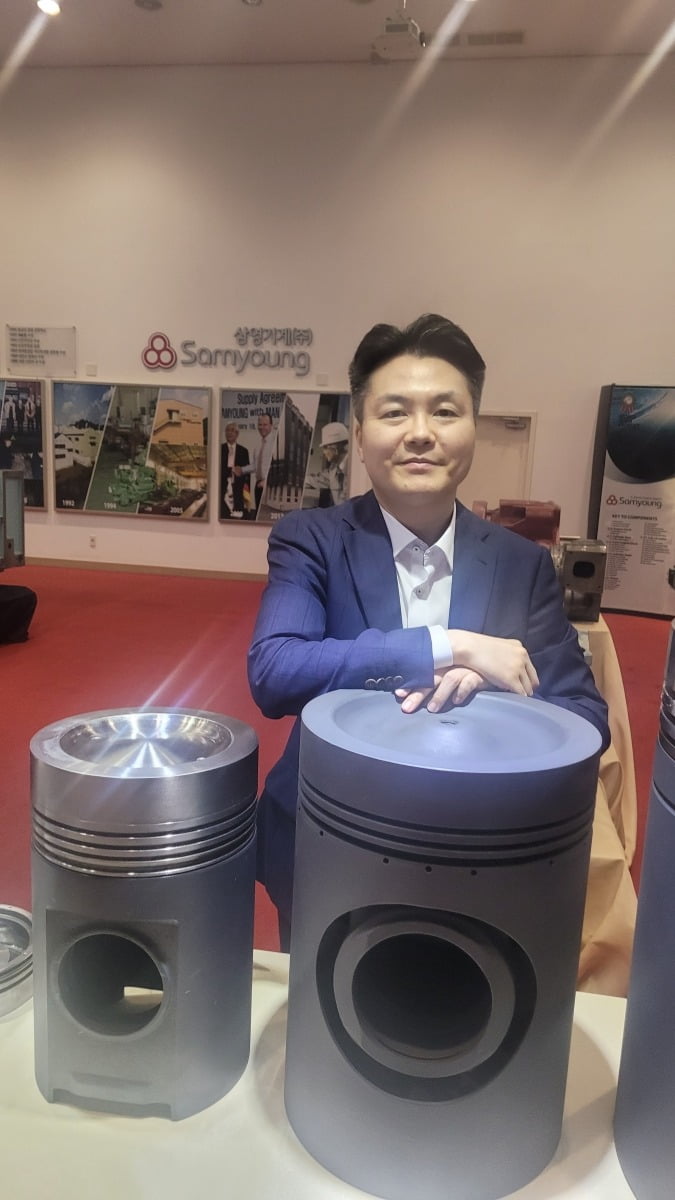
삼영기계는 3D 프린터를 통해 현장 수작업의 40~60% 절감 효과를 거뒀다. 시제품 제작 기간도 대폭 단축됐다. 한 사장은 “3D 프린터로 제품을 만들면 훨씬 복잡한 형태의 제품 설계도 가능할 뿐 아니라, 주조 공정 과정에 소요되는 에너지를 대폭 절감하여 탄소저감 효과도 기대할 수 있다”며 “열악한 작업환경과 인력난에 시달리는 뿌리기업이 지속가능할 수 있는 가장 효과적인 수단은 디지털 전환에 달려 있다”고 덧붙였다. 한 사장은 뿌리산업 발전 공로를 인정받아 이달 산업통상자원부 장관상을 수상한다.
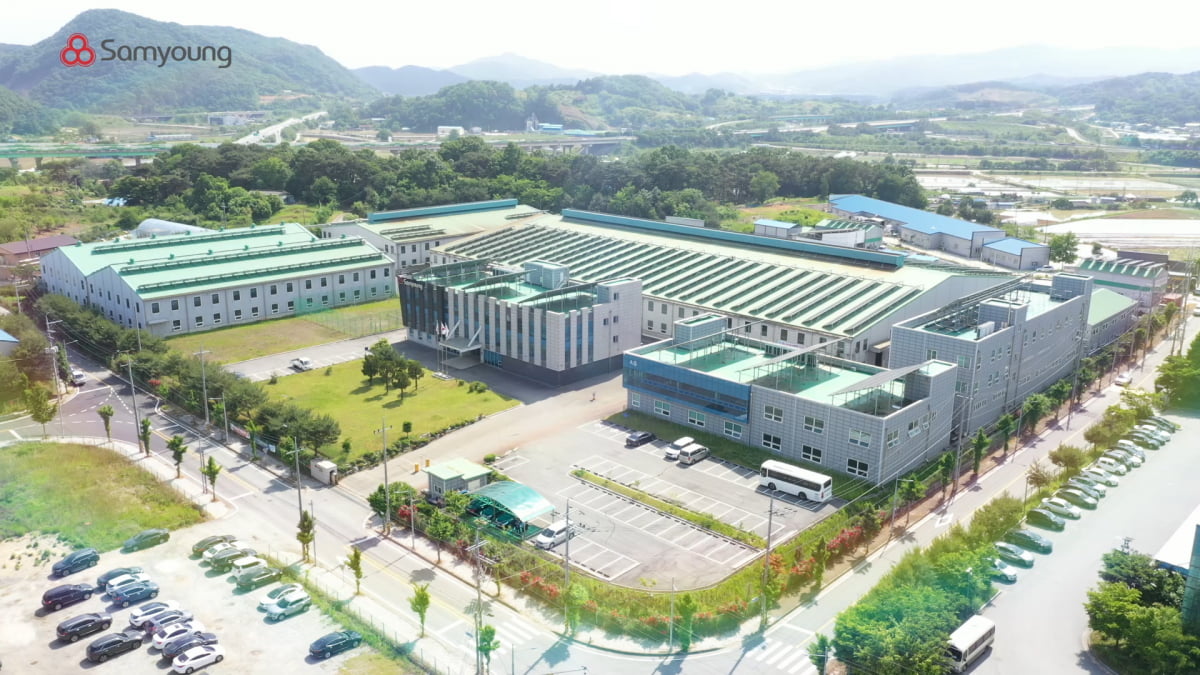
공주=이정선 중기선임기자