"극한날씨에 어떻게 멀쩡하죠?"…현대차·기아 비밀기지 가보니 [현장+]
-
기사 스크랩
-
공유
-
댓글
-
클린뷰
-
프린트
현대차·기아 비밀 기지를 가다
"10년 타도 변함 없는 성능 개발"
현대차·기아 남양기술연구소 견학
신차 및 신기술 개발은 물론 디자인·설계·시험·평가 등 기반 연구시설 갖춰
전동화 차량 개발 핵심 연구 시설 공개 통해 앞선 기술력 자랑
"10년 타도 변함 없는 성능 개발"
현대차·기아 남양기술연구소 견학
신차 및 신기술 개발은 물론 디자인·설계·시험·평가 등 기반 연구시설 갖춰
전동화 차량 개발 핵심 연구 시설 공개 통해 앞선 기술력 자랑
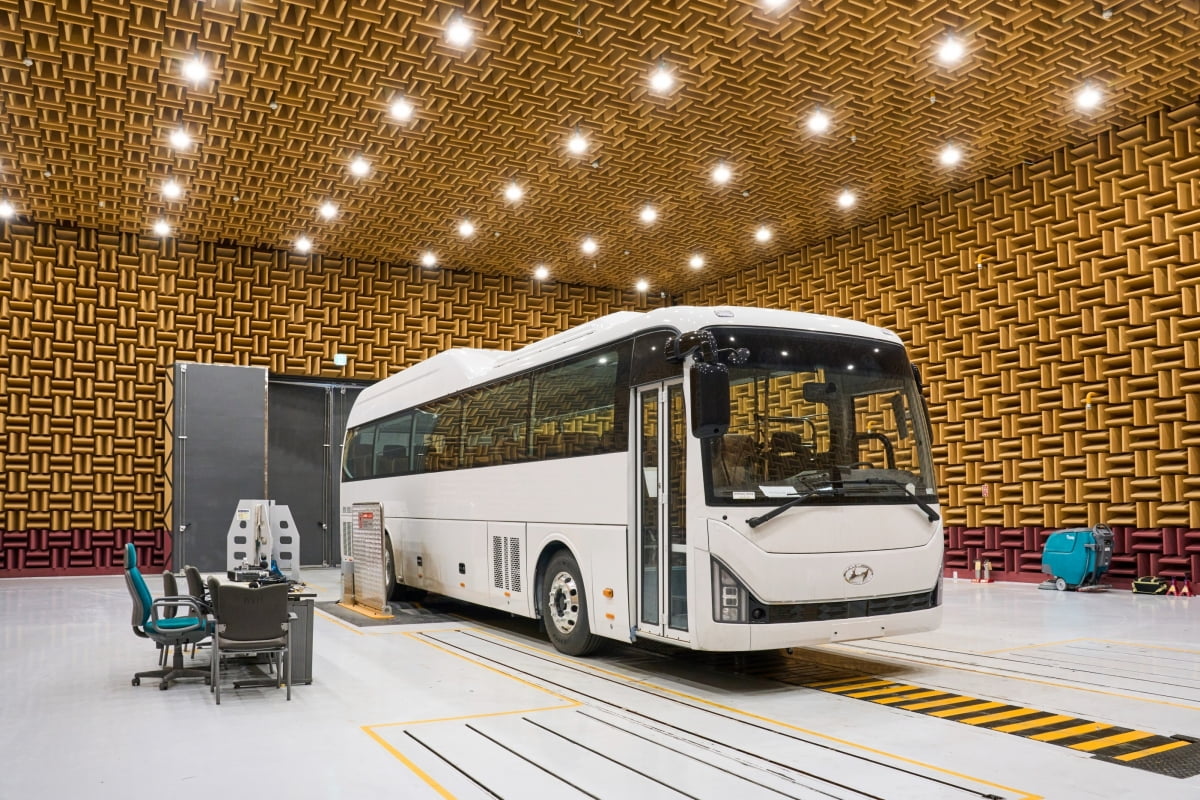
입구에 들어서자마자 휴대폰과 노트북 카메라에 보안 스티커를 붙이는 철통 보안을 거쳐 연구소에 들어설 수 있었다. 버스를 타고 이동해야 할 정도로 큰 부지는 기존 세상과 동떨어진 새로운 세계처럼 느껴졌다. 연구소 내 도로에는 현대차와 기아의 브랜드를 달고 나올 차량들이 위장막에 가려진 채 도로를 달리고 있었다.
경기도 화성시에 위치한 남양연구소는 1995년 출범한 종합기술연구소로 승용·상용 등 전 차종에 대한 연구개발을 책임지고 있다. 신차 및 신기술 개발은 물론 디자인, 설계, 시험, 평가 등 기반 연구시설을 두루 갖추고 있다.
최근에는 전동화 트렌드에 발맞춰 전기차, 수소전기차 개발 역량에 초점을 맞추고 있다. 이번 방문에서는 남양연구소의 차량 개발의 주요 프로세스를 담당하는 △상용시스템시험동 △전기차 동력계 시험실 △배터리 분석실 △상용환경풍동실을 둘러봤다.
상용시스템시험동, 운전자 위한 모든 조건 평가
가장 먼저 둘러본 곳은 상용시스템시험동으로 현대차·기아의 모든 상용차는 이곳에서 혹독한 시험을 거쳐 개발된다. 평가 조건은 일부 다르겠지만 구조적으로는 승용차 시험 연구와 거의 동일한 프로세스로 볼 수 있다.4400여평에 달하는 면적으로 국내 최대 규모를 자랑하는 거대한 시험동에서는 실차 거동 재현과 필드 환경을 반영한 차량 평가 검증이 한창이었다.
일직선으로 길게 뻗은 시험동 내부는 차체·안전, 조향·현가, 구동·제동, 품질·내구, 소음·진동·혹독함(NVH) 등 크게 다섯 가지 구역으로 이뤄졌다. 차체·안전 구역에서는 차량 내외부의 안전을 테스트하는 충돌 시험과 기후환경을 재현한 시험 장비들을 볼 수 있었다.
로봇시험실에 들어서자 로봇 팔이 차 문을 일정한 강도로 열고 닫기를 반복하며 부품의 내구성을 시험하는 테스트가 진행 중이었다. 담당 연구원에 따르면 문을 여닫는 강도는 실제 사람의 힘과 동일하며 충분한 내구성 데이터 확보를 위해 로봇이 24시간 내내 몇 달간 시험을 계속하는 경우도 있다고 했다. 상용시스템시험동에서 진행되는 대부분의 시험은 이처럼 필드 조사 결과에 기반해 실제와 비슷한 조건으로 진행된다.
조향·현가 구역에서는 거대한 장비들이 굉음을 내며 돌아가고 있었다. 한쪽에는 유압 액추에이터로 구동되는 육중한 로봇이 전기버스 일렉시티의 서스펜션을 연신 흔들며 서스펜션의 내구성을 시험하고 있었다. 타이어에 직접 하중을 가하며 로봇이 다양한 방향의 움직임과 회전을 구사할 수 있어 혹독한 상황을 가정한 테스트가 가능하다는 게 연구소 측의 설명이다.
여러 설비를 지나 상용시스템시험동의 마지막 구역인 NVH 다이나모 무향실에 도착했다. 문을 열고 안으로 입장하자 1만3000개의 흡음재로 빼곡히 둘러싸인 7.5m 높이의 방음벽이 눈에 들어왔다. NVH 구역에서는 엔진 구동계 소음부터 실내외 소음까지 실제 차량에서 발생할 수 있는 모든 소음을 평가한다.
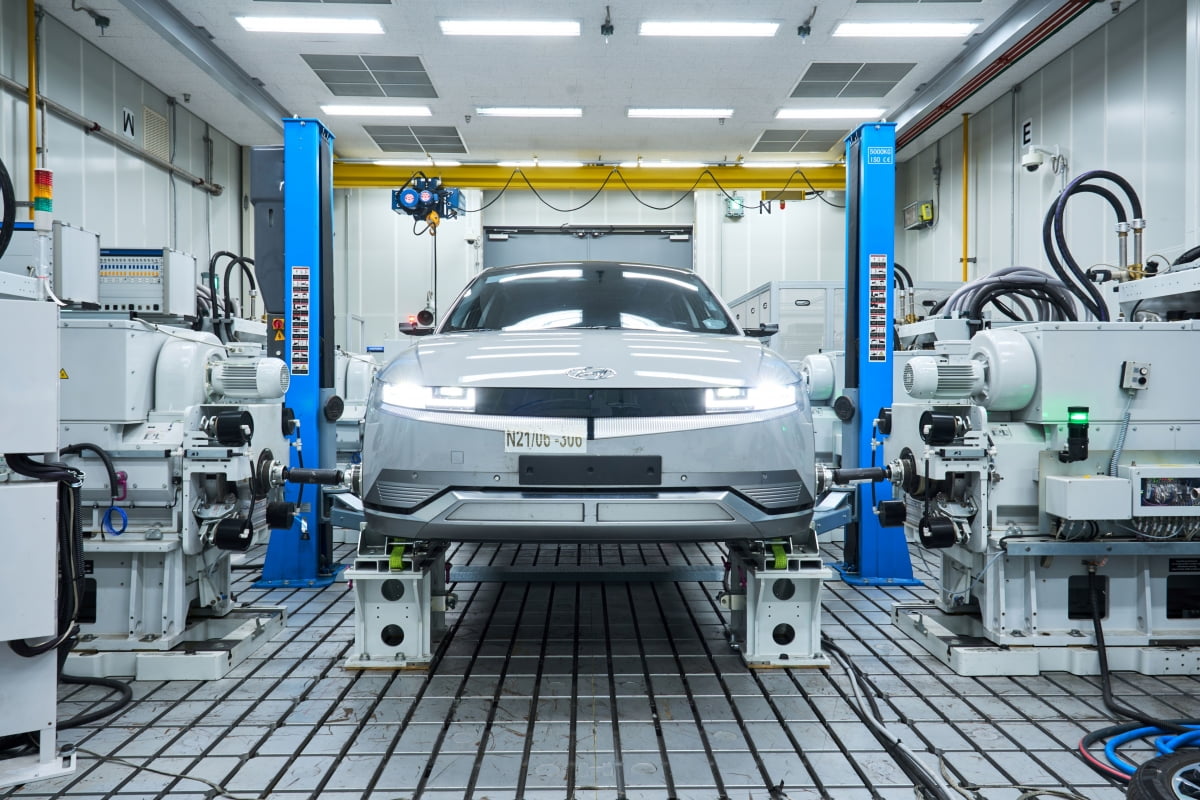
전기차 심장 개발하는 '전기차 동력계 시험실'
다음으로 방문한 곳은 전기차 동력계 시험실로 전기차 핵심 구동계인 모터와 인버터의 성능을 사전 개발하고 실차 효율을 평가해 전기차가 최적의 성능을 발휘할 수 있도록 하는 곳이다.이 시험실은 실제 도로에서 이뤄지는 주행 테스트와는 달리 실내 시험 공간 내에서 가혹한 테스트를 반복해서 진행할 수 있다. 다양한 상황과 조건을 모사해 개발 과정에서 발생하는 문제에 대한 신속한 원인 파악과 개선으로 EV의 품질 제고 및 강건화를 가능하게 한다.
시험실에 들어서자 좌우에 위치한 여러 개의 시험실 유리창 너머로 '위이잉' 대는 모터 소리가 들려왔다. 총 3곳으로 이루어진 시험실 내부에는 모터와 인버터를 측정하는 커다란 장비들이, 그리고 한쪽에는 현대차 아이오닉 5 차량이 장비에 맞물려 있었다.
동력계 시험실은 1축, 2축, 4축 동력계 시험실로 나눠져 있는데 1축 동력계 시험실은 모터와 인버터의 기본 특성에 대한 시험을 하는 곳으로 단품 시험이 이뤄지는 곳이다. 주로 차량 개발 초기 단계에 이뤄지는 시험으로 모터 시스템의 성능, 효율 개발을 목적으로 한다. 2축 동력계 시험실은 모터와 인버터에 감속기, 구동축을 추가해 실제 차량의 구동계를 모사한 환경이 구축돼 있다. 파워 일렉트릭(PE, Power Electric) 시스템 전체의 효율과 매핑, 냉각, 열해 시험으로 필드에서 발생할 수 있는 문제를 사전 검증하는 것을 목적으로 한다.
4축 동력계 시험실은 실체 차량을 직접 구동해 사륜구동(AWD, All wheel drive) 포함 구동계 전체의 시험 평가가 가능한 곳이다. 배터리 시뮬레이터를 사용했던 1, 2축 시험실과 달리 전기차에 탑재되는 실제 배터리를 직접 활용하며 고객의 주행 환경과 동일한 조건에서 평가가 이루어지기 때문에 모든 영역에서의 EV 성능을 가장 정확하게 검증할 수 있다.
이 시험실에서 눈에 띄는 점은 운전석에 로봇이 기어, 액셀, 브레이크 등을 조작하고 있다는 점이다. 운전자의 역할을 대체하는 이 로봇은 가속과 제동을 위해 페달을 밟는 동작을 사람과 유사하게 따라 하고 심지어 자동으로 변속까지 할 수 있다.
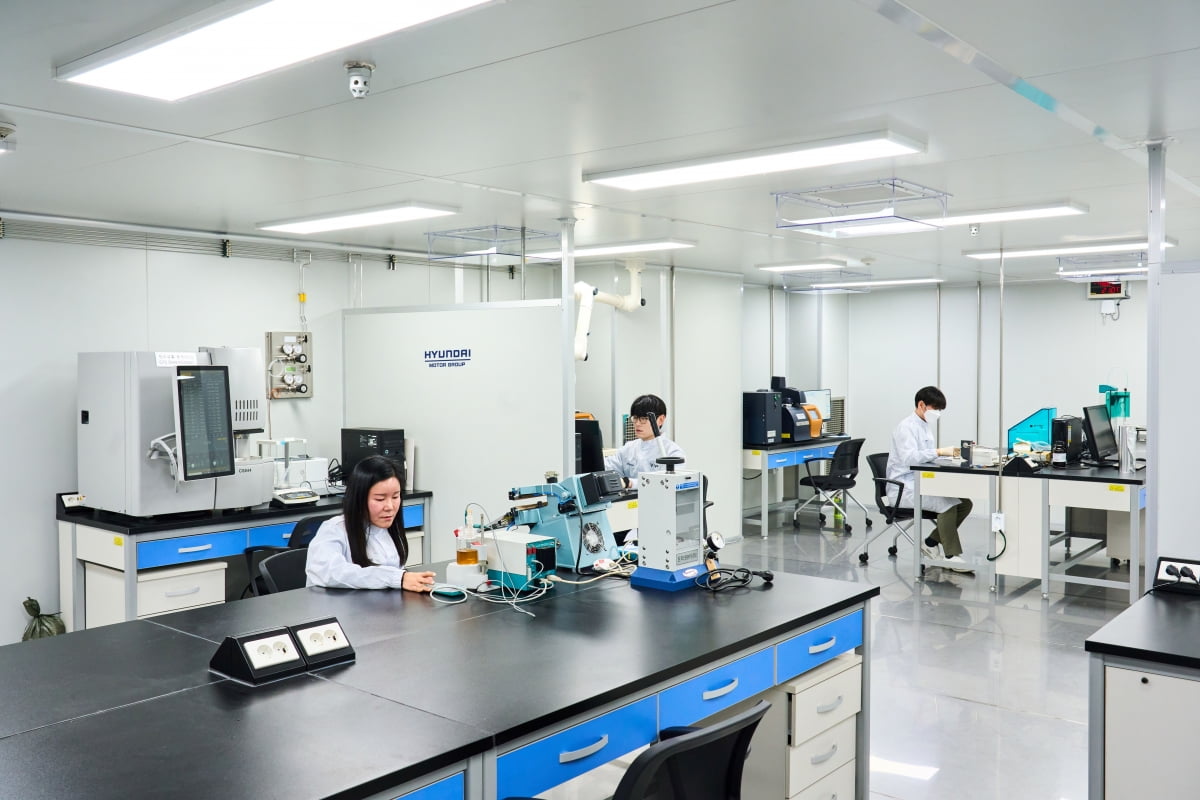
배터리 분석실, 차세대 배터리 기술 내재화의 중심
세 번째로 방문한 곳은 배터리 분석실로 전기차의 핵심 부품인 배터리를 분석해 세부 구성 물질을 연구하는 곳이다. 배터리 셀을 구성하는 소재에 대한 정밀 분석을 통해 셀의 성능, 내구성, 안정성 등을 전체적으로 평가한다. 현대차·기아가 자체 연구하고 있는 차세대 배터리에 적용될 신규 소재에 대한 분석도 진행하고 있다는 게 관계자들의 설명이다.배터리 분석실은 소재 연구 특성상 온·습도가 일정하게 유지되는 드라이룸 환경 하에 운영되고 있었다. 실제로 이날은 기자들의 견학을 위해 드라이룸 기능을 해제한 상태였음에도 불구하고 다른 공간보다 건조함이 느껴졌다.
이재욱 재료분석팀 팀장은 "전기차 배터리는 소재 특성상 수분에 매우 민감하기 때문에 일정 온도와 습도 조건을 유지하는 것이 중요하다"며 "드라이룸이라는 특수환경에서 셀을 해체하고 분석을 진행해야 신뢰성 있는 분석 결과를 확보할 수 있기 때문"이라고 설명했다.
분석을 위해 배터리가 처음 옮겨지는 장소는 '셀 해체실'이다. 배터리 셀의 구조 파악과 구성 소재 분석을 위한 시료 채취 작업이 진행된다. 셀 해체실 공간은 혹시 모를 화재 위험을 방지하기 위해 바닥, 벽면, 천장을 비롯해 테이블과 같은 기본 설비 모두 스테인리스 스틸 소재로 마감돼 있다. 또 해체실 한편에는 자동소화 설비가 적용된 흄후드와 각종 화재 차단 설비가 곳곳에 비치돼 있다.
분석 장비 가운데 레이저 광원을 활용, 물질 간 결합을 분석하는 라만분광분석기를 자세히 살펴볼 수 있었다. 시료 표면에 레이저를 쬐어 나온 신호를 기반으로 물질 특성을 분석하는 장비로 반도체 웨이퍼나 배터리 분리막 코팅 소재 등의 구조 분석에도 활용된다고 한다.
이외에도 배터리 분석실에서는 다양한 시험을 통해 배터리 설계 사양 및 내구성, 충·방전 조건에 따른 성능과 수명 평가 등을 확인하며 필드에서 발생할 수 있는 모든 품질 문제에 대응한다. 또 현대차·기아가 자체 연구 중인 차세대 배터리에 적용될 신규 소재에 대한 분석도 진행하고 있다.
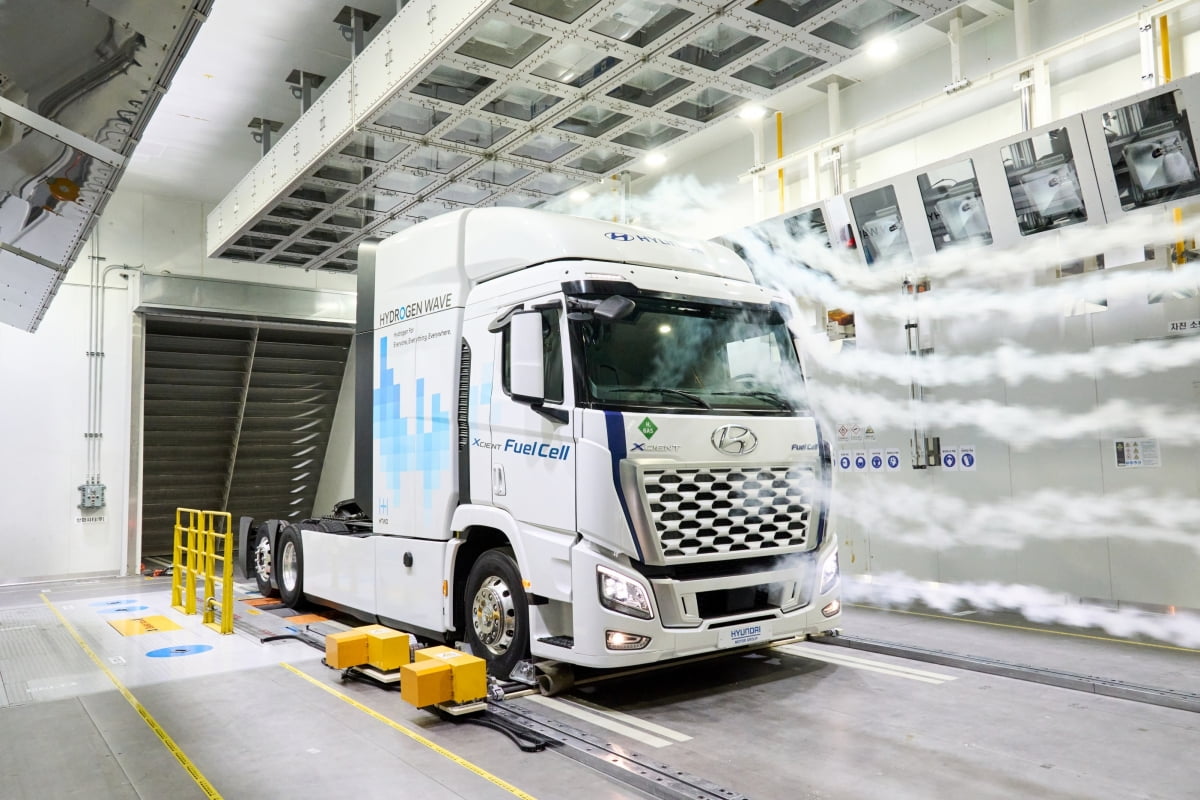
극한의 환경 구현한 상용환경풍동실…실차 주행 성능시험 진행
이번 투어에서 기자의 시선을 가장 크게 사로 잡은 곳은 상용환경풍동실이었다. 환경풍동시험실에서는 냉각, 열해, 연비, 냉시동, 히터·에어컨, 충·방전, 동력, 모드 주행, 배기가스인증 등 실차 주행 성능시험을 종합적으로 진행할 수 있다.실내 온도를 –40℃~ 60℃까지, 습도를 5%~ 95%까지 조절할 수 있어 세계 곳곳의 날씨는 물론, 극한 환경까지 재현 가능하다는 점이 큰 특징이다. 더욱이 3.3m의 대형 팬으로 시속 120km에 달하는 기류를 만들어 실제 주행 조건과 동일한 시험도 할 수 있다.
제어실로 입장하자 엑시언트 수소전기 트럭이 비치된 환경풍동실이 눈앞에 펼쳐졌다. 환경풍동실 내부 공간은 길이 20m, 너비 10m, 높이 6.6m에 달할 정도로 세계 최대 규모를 자랑한다. 풍동실 내부 천장 및 측면에 태양광(Solar) 장비가 설치돼 있어 마치 화창한 여름날 야외 풍경을 보는 듯한 느낌이 들었다.
실제로 풍동실 안에 들어가 보니 후덥지근한 열기가 느껴졌다. 시험실 온도가 중동 지역 테스트 기준 온도인 45℃에 맞춰져 있었기 때문이었다. 실제 45℃ 환경에 방치한 자동차의 실내 온도는 보통 60℃ 이상으로 올라가는데 상부의 태양광 시스템이 이와 같은 온실효과를 동일하게 재현하여 미국 현지 판매 조건으로 시험을 했다.
이날 현장에서는 고온 조건 테스트 시연과 함께 유동 가시화 시험을 실제로 지켜볼 수 있었다. 유동 가시화 시험은 풍동 내부에 가스를 분사시켜 차량 주변의 공기 흐름을 확인함으로써 공력성능 향상에 기여하는 테스트이다.
환경풍동시험실은 상용 전기차 및 수소차를 전문적으로 연구하는 시설인 만큼 최첨단 안전시스템을 갖추고 있다. 시험실 내부 모든 시설물은 수소 방폭 설비로 되어 있으며 화재를 방지하기 위한 각종 감지기(열·연기·불꽃·수소 등)와 자진 소화 설비까지 갖추고 있다. 이러한 노력 덕분에 과학기술정보통신부와 국가연구 안전관리본부에서 인증하는 '안전관리 우수연구실' 자격도 실차를 시험하는 시험실로는 최초로 획득했다.
견학을 다 마치고 나오는 길에 남양연구소 한 건물 밖에 '10년을 타도 변함 없는 내구성능 개발'이라는 글귀가 쓰여져 있었다. 기술 혁신과 경쟁력 향상을 통해 글로벌 시장에서의 입지와 영향력을 강화해 나가는 현대차그룹의 노력을 확인할 수 있는 시간이었다. 지금도 현대차·기아는 남양연구소에서 전동화에 대한 치열한 연구를 거듭하며 전기차 시장을 선도하는 동시에 글로벌 게임체인저로 거듭나고 있는 중이다.
차은지 한경닷컴 기자 chachacha@hankyung.com