차량 '콕핏'의 진화…가볍고 튼튼한 복합소재로 승객 안전 지킨다
-
기사 스크랩
-
공유
-
댓글
-
클린뷰
-
프린트
현대모비스 부품이야기
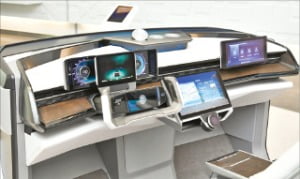
고객이 차량의 디자인을 평가할 땐 외부 익스테리어가 가장 우선이 되겠지만, 차량에 탑승해 계속 생활하는 부분은 내부 인테리어에 달렸다. 특히 전방에 자리한 콕핏을 가장 많이 본다.
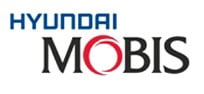
최근에는 대화면 디스플레이를 통해 다양한 정보를 제공하는 콕핏 시스템의 개발도 이뤄지고 있다. 다양한 조명을 통해 미래 지향적인 이미지를 구현한다. 사람의 습관이나 생체 리듬을 분석하고 최상의 조건으로 이끌어준다.
이런 새로운 표현과 기능을 위해 요즘 차들의 콕핏 구성은 과거와 많이 달라졌다. 커다란 디스플레이가 장착된다. 다양한 곳에서 직간접 조명이 구현된다. 기존 콕핏을 구성하던 부품들은 원래 기능은 유지하면서 고급스러움은 높이고 중량은 줄여야 한다. 제조 비용을 낮춰야 하는 숙제도 있다. 이를 위해 연구소에선 제품의 형상 설계만이 아니라 다양한 재료 기술과 성형 기술을 습득하고 이를 융합한다. 최적의 제조 원가로 탄생시키기 위한 다양한 선행 개발 활동을 시행한다.
고급스러운 가죽이 감싸져 있고 여러 부품이 장착된 크래시패드(대시보드)가 대표적이다. 특히 크래시패드 코어라고 부르는 부품은 저비중 고강성 소재 기술과 발포 사출 성형 기술이 융합돼 탄생했다.
크래시패드 코어는 보통 폴리프로필렌(PP)이라고 불리는 재료에 고무나 무기필러를 혼합해 만든다. 원래는 물질의 밀도를 나타내는 단위인 비중이 1보다 높게 형성된다. 그러나 일부 특수한 필러를 혼합할 경우 0.95 수준의 비중을 형성하면서 부품이 요구하는 기계적 강도를 만족시킬 수 있다.
여기에 더해 사출 성형 시 금형 내부에 기체를 같이 주입해 스펀지와 같은 다공체 구조를 형성할 수도 있다. 인체의 뼈와 같은 형태다. 뼈는 유기 성분인 콜라겐과 칼슘, 인산 등의 무기 성분으로 구성된다. 단단한 무기 성분은 압축력을 증가시켜 무거운 무게를 잘 견딘다. 유기 성분은 탄성과 장력을 높여 질겨진다. 뼈가 다공체 구조임에도 튼튼한 이유가 유기 성분과 무기 성분이 최적의 구조로 형성돼 있기 때문이다.
이렇게 형성된 크래시패드의 비중은 0.9 이하로 형성된다. 비중이 1인 물보다 가벼우면서 튼튼한 구조물이 되는 것이다. 이 같은 복합소재의 제품은 혹서, 혹한, 다습 조건에서도 변형이 되지 않는다. 소재의 강도가 높기 때문에 사고 시 승객을 보호하는 측면에서도 효과적이라고 할 수 있다.
미래엔 완전 자율 주행이 실현될 것이다. 이때 운전을 하지 않기 때문에 콕핏은 다른 형태로 바뀔 것이다. 그러나 차량을 제어하는 방식이 바뀌는 것이지, 승객의 안전을 책임지고 차량의 인테리어를 고급스럽게 만드는 방식은 계속된다. 이런 차량 콕핏 모듈 기술의 발전을 위해 연구원들은 설계 구조를 최적화하고, 합리적인 재료 선정과 효율적인 가공 기술에 대한 연구를 지속적으로 하고 있다.
현대모비스 기술연구소