매출 3배 껑충 뛴 이 회사, 전고체 배터리 장비로 불황 넘는다 [최형창의 中企인사이드]
-
기사 스크랩
-
공유
-
댓글
-
클린뷰
-
프린트
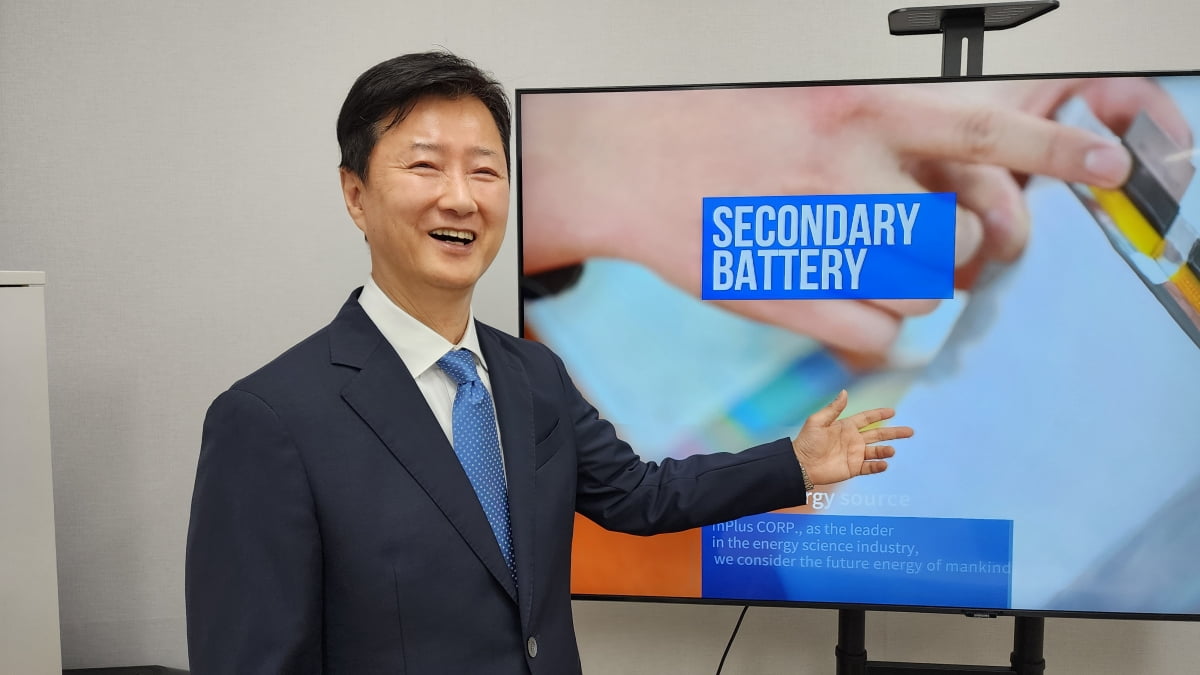
김 대표는 삼성SDI에 근무할 당시 리튬이온 배터리 국산화를 이뤄낸 인물 중 한 명이다. 함께 근무한 동료들과 디스플레이의 한 종류인 플라즈마디스플레이(PDP) 제작을 위한 초음파 스크라이빙 장비를 국산화하겠다고 결심한 뒤 2003년 엠플러스를 창업했다. 회사는 세웠지만, 사업화하기까지는 쉽지 않았다. PDP시장 수요가 사라지면서 회사는 자본잠식 위기까지 몰렸다. 하지만 미국 A123시스템즈에서 세계 최초 전기차용 파우치형 배터리 조립라인 수요가 발생했고, 엠플러스는 이 사업을 단독 수주해 기사회생했다.
엠플러스는 이차전지 조립공정 전체를 일괄 도입(턴키) 방식으로 제작할 수 있는 세계 유일한 회사다. 김 대표는 “공정 전체를 턴키로 공급하면 각 장비 별로 발생할 수 있는 규격 조정 문제가 해소되고, 공정간 물류 흐름의 최적화를 이룰 수 있다”며 “납품 받는 거래처 입장에서도 공정의 불량률을 줄이고, 관련 비용을 최소화할 수 있어 서로 윈-윈”이라고 강조했다.
배터리 안에 들어가는 양극판·음극판을 안정적이면서도 빠른 속도로 쌓을 수 있는 장비 기술력도 엠플러스의 경쟁력이다. 김 대표는 “배터리 하나를 만들 때 빠르게 배터리셀에 맞는 양극판과 음극판을 노칭 가공해야 하는데 분당 300장까지 가공할 수 있어서 배터리 제조 업체입장에선 굉장히 생산성을 높일 수 있는 시스템”이라고 밝혔다.
전기차 수요 감소 여파로 전세계 배터리 시장이 정체기를 맞았지만, 엠플러스는 차세대 전고체 배터리 생산장비로 사업 영역을 넓혀 새 활로를 찾고 있다. 전고체 배터리는 양극과 음극 사이 전해질을 액체에서 고체로 바꾼 배터리다. 발화나 폭발 위험이 없어 안전성이 우수하고 에너지 밀도가 높아 꿈의 배터리로 불린다. 김 대표는 “전고체 배터리 핵심공정 장비를 개발해 상용화를 앞뒀다”면서 “올해 하반기 미국 전고체 배터리 개발기업에 장비를 공급할 예정”이라고 말했다.
최형창 기자 calling@hankyung.com