리튬이온배터리 분리막 얇게 더 얇게…R&D 경쟁
-
기사 스크랩
-
공유
-
댓글
-
클린뷰
-
프린트
분리막은 배터리 안정성 담당
양극과 음극 접촉 않도록 막아
리튬이온 왕래하는 통로 역할도
두께 얇을수록 에너지 밀도 높아
LG화학, 일본 도레이와 합작생산
삼성SDI는 분리막 코팅기술 내재화
양극과 음극 접촉 않도록 막아
리튬이온 왕래하는 통로 역할도
두께 얇을수록 에너지 밀도 높아
LG화학, 일본 도레이와 합작생산
삼성SDI는 분리막 코팅기술 내재화
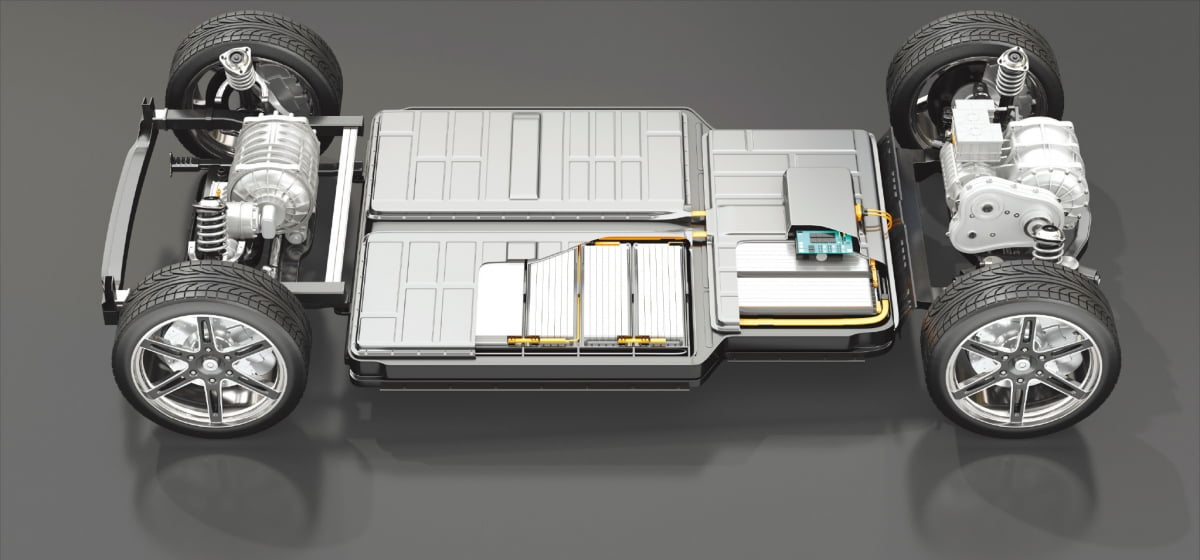
○배터리 안정성 높이는 분리막
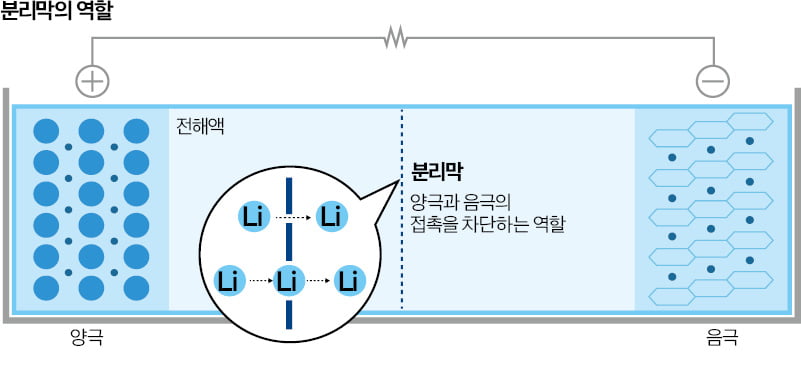
분리막의 역할 자체는 배터리 용량과 무관하다. 하지만 분리막의 두께가 얇으면 같은 부피 내 양극과 음극 활물질을 더 넣어 에너지 밀도를 높일 수 있다. 그래서 분리막 두께를 줄이는 연구도 많이 진행되고 있다. 배터리에서 사용하는 박막 분리막의 두께는 5~30마이크로미터(㎛)로 매우 얇다. 기공의 크기는 10~500나노미터(㎚) 정도다. 배터리업체들은 기계적 강도는 더 높으면서 두께는 더 얇은 분리막 개발에 공을 들이고 있다.
분리막 제조 방식은 습식과 건식 두 가지로 나뉜다. 리튬이온이 오가는 기공을 어떻게 만드느냐에 따라 갈린다. 건식 제조는 필름 원단을 당겨 폴리프로필렌(PP)이나 폴리에틸렌(PE) 결정의 계면 사이를 벌려 기공을 만드는 방식이다. 비교적 제조 공정이 간단하다. 습식 제조는 PE에 기름을 섞고 여러 첨가제를 넣어 고온과 고압으로 반죽해 필름을 뽑아내는 방식이다. 이후 분리막을 냉각해 성형할 때, PE와 기름이 분리된다. 그 기름을 용매 추출로 뽑아내면 그 빈 자리가 기공이 된다.
코팅을 통해 분리막의 안전성은 한층 높아졌다. 코팅 방식은 내열 코팅과 접착 코팅으로 나뉜다. 내열 코팅은 분리막 원단 필름에 고내열 바인더와 세라믹 입자를 코팅해 원단의 수축을 억제한다. 접착 코팅은 분리막 원단 필름에 접착 바인더를 코팅하고 이를 극판과 접착해 안전성을 높이고 변형을 방지하는 방식이다.
국내 분리막 기업으로는 SK아이이테크놀로지, 더블유씨피, LG화학이 있다. LG화학은 일본 도레이와 합작공장 형태로 분리막을 생산 중이다. 삼성SDI는 분리막 코팅 기술을 내재화했다. 2013년 자체 연구개발을 시작해 2014년 구미사업장에 분리막 생산라인을 지었다. 이 회사는 분리막 표면에 세라믹 코팅, 바인딩 코팅을 동시에 하는 ‘고내열성 접착 분리막’을 개발한 바 있다.
○리튬의 ‘운하’ 전해질
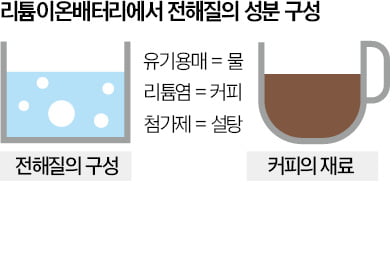
리튬이온배터리 대부분은 액체 상태의 전해질(전해액)을 사용하고 있다. 리튬염이 유기용매에 녹아 있는 형태다. 배터리를 충전할 때 이온화된 리튬은 전해질을 통해 음극으로 이동하고 음극재(흑연)에 자리 잡는다. 전해질이 통로 역할을 하는 것이다. 통상 배터리 원리를 설명하는 그래픽을 보면 리튬이온이 전해질을 헤엄쳐 이동하는 식으로 묘사한다. 그러나 정확하게는 리튬이 전달되는 것이기에 통로가 아니라 ‘통로 역할’을 한다. 양극에서 빠져나온 리튬이온이 전해질에 녹아 있는 리튬을 밀면서 음극으로 전달되는 구조라서다. 배터리가 방전될 때는 반대다. 음극재에 있던 리튬이온이 전해질로 나오면 기존에 전해질에 녹아 있던 리튬이온이 한 자리씩 밀리고 밀려 양극재 안으로 복귀한다.
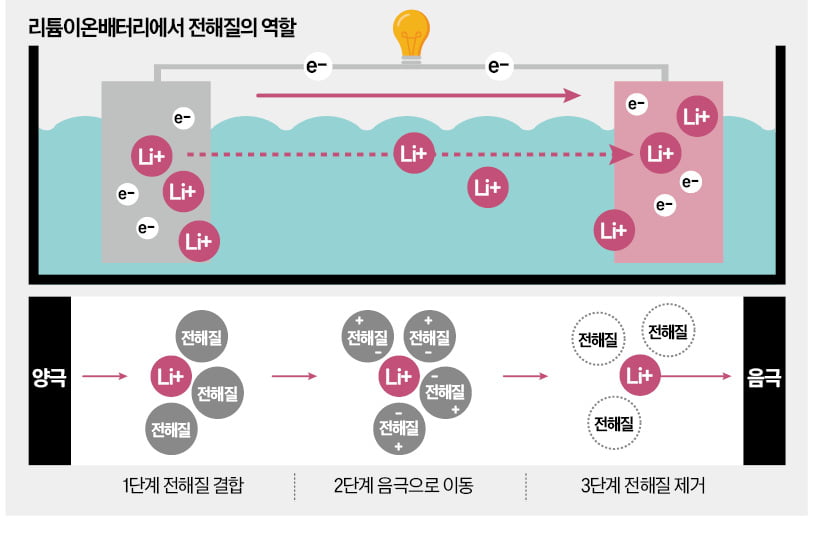
일상에서 쓰는 아세톤, 에탄올 등인 유기용매는 리튬염을 녹이는 액체다. 리튬은 물과 만나면 반응이 크게 나타나는 금속이라 유기용매를 사용한다. 유기용매는 물에 잘 녹지 않고 휘발이 잘되며 세정력이 좋고 특이한 냄새가 난다. 전해질의 유기용매는 리튬염을 잘 녹여 리튬이온이 원활히 이동하도록 도와준다.
설탕 역할의 첨가제는 특정 목적으로 소량만 쓰는데, 배터리의 안전성 및 성능 관련 여러 기능을 한다. 충·방전 과정에서 발생하는 배터리 문제를 첨가제로 해결하려는 것이다. 첨가제는 양극용과 음극용으로 나뉜다. 양극용 첨가제는 양극의 구조를 안정화하거나 표면을 보호한다. 이를 통해 열화를 억제하고 발열 현상을 개선해 과충전을 방지한다. 음극용 첨가제는 음극에 튼튼한 막을 형성하고 수명을 늘린다. 또 발열을 줄이거나 용량을 유지해 가스 발생을 줄인다.
양극용과 음극용 첨가제는 모두 용매에 잘 녹고 화학적으로 안정성이 있어야 한다. 배터리가 요구하는 스펙에 따라 달리 적용된다. 요즘엔 고전압 배터리 수요가 느는 데 따라 양극과 음극을 모두 보호하는 첨가제를 개발하고 있다. 배터리 생산 중에 들어간 이물을 제어해 불량을 잡아주는 첨가제도 있다. 정리하자면 첨가제는 전해질에서 절대적인 함량을 차지하지는 않지만 수명 개선, 고온 특성 개선, 저항 감소 등 전해질 전체 시스템에서 핵심적인 역할을 한다.
김형규 기자/도움말=삼성SDI 뉴스레터