"내 덕에 아이폰6 나온 셈"…칼에 미친 사장님의 '진검승부' [중기열전]
-
기사 스크랩
-
공유
-
댓글
-
클린뷰
-
프린트
조재연 엔티이엔지 대표
!["내 덕에 아이폰6 나온 셈"…칼에 미친 사장님의 '진검승부' [중기열전]](https://img.hankyung.com/photo/202412/01.38811520.1.jpg)
당시 조재연 엔티이엔지 대표(사진)가 요청받은 제품은 두께가 이전 제품의 절반 수준(0.28㎜)에 불과한 도광판(LGP. 백라이트 유니트 부품의 균일한 조명기능을 수행하는 핵심 부품)을 자를 수 있는 절단기였다. 도광판은 화면의 빛을 균일하게 분포하기 위해 LCD 백라이트에 사용되는 핵심 부품이다. 단면이 깨끗해야 빛을 균일하게 산란해 해상도를 유지할 수 있다.
문제는 이처럼 얇은 도광판을 절단하려면 그만큼 정교한 절단기가 필요하다는 점이었다. 연마(고속 가공) 방식으로는 깨끗한 절단이 불가능했고 무딘 칼날을 사용하면 도광판의 단면이 울퉁불퉁해지거나 아예 깨지기 일쑤였다.
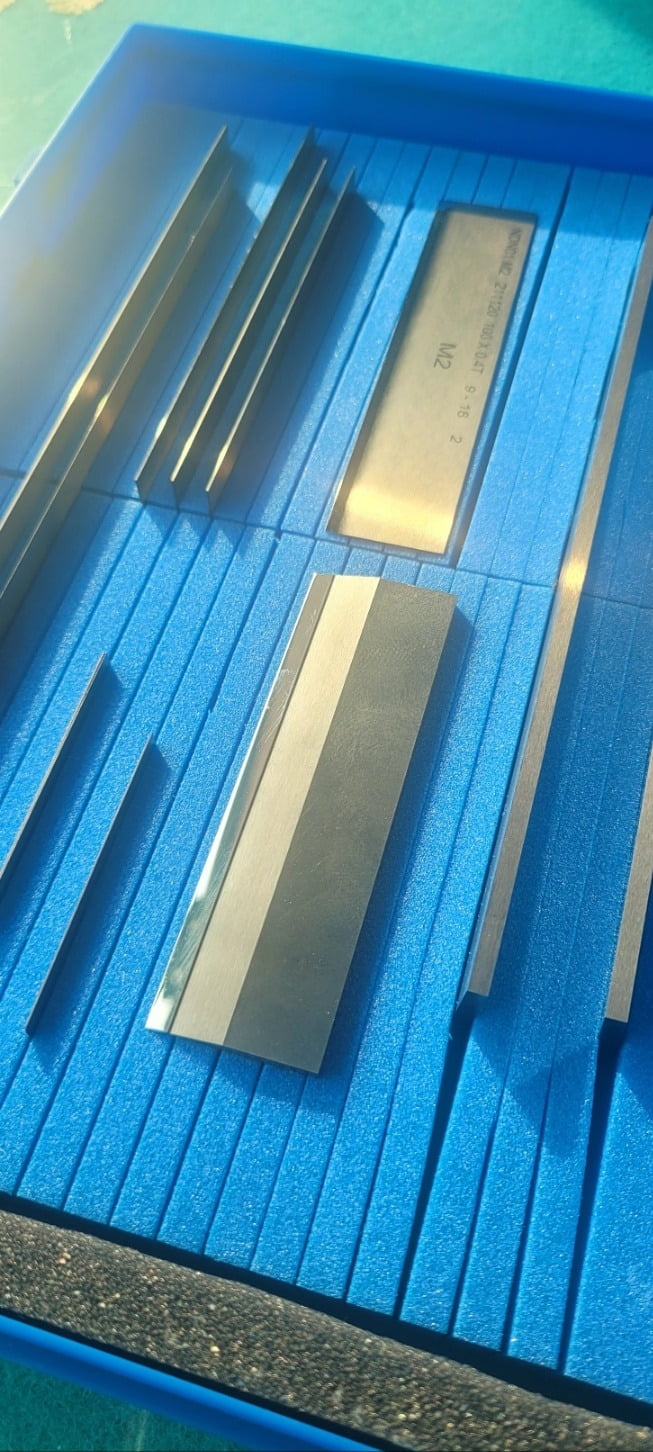
조 대표는 우선 칼날의 특성을 이해하기 위해 전국의 대장장이부터 쫓아다녔다. 공업용 블레이드를 잘 만든다고 알려진 엔지니어와 전문가들도 찾아다녔다. 수개월간 수십 명의 장인들로부터 그가 터득한 원리는 이랬다. 정밀한 칼날을 구현하기 위해선 표면의 거칠기를 유리처럼 가공하는 것은 물론 제품의 특성에 따라 칼날의 끝 선(刃先)을 달리해야 하는 기술이 핵심이었다.
장비 개발에는 이골이 나 있던 그는 곧 칼날 제작에 착수했다. 조 대표는 2001년 자동화 기계 전문 엔티이엔지를 설립한 뒤 대당 5000만 원이 넘는 장비를 300종 이상 개발한 이력을 갖추고 있었다. 소재 검사장비, 자동차부품 제조 장비, 모바일 자동화 장비, 의료·바이오 장비 등 그가 다루지 않은 산업 분야는 거의 없다.
!["내 덕에 아이폰6 나온 셈"…칼에 미친 사장님의 '진검승부' [중기열전]](https://img.hankyung.com/photo/202412/01.38811481.1.jpg)
엔티이엔지가 독점 제작한 대당 1억 원 안팎의 초정밀 절단기는 백라이트를 사용하는 여타 국내외 스마트 제조업체의 협력사에 날개 돋친 듯이 팔려나갔다. 엔티이엔지의 초정밀 절단기의 호황은 3~4년을 채 넘기지 못했다. 자체 발광 방식의 OLED가 나오면서다.
그렇게 묻히는가 싶었던 조 대표의 블레이드는 적층세라믹콘덴서(MLCC)용 초정밀 절단기 수요가 늘면서 다시 빛을 보기 시작했다. MLCC는 전기를 저장했다가 일정량 내보내는 댐의 기능을 하는 장치다.
엔티이엔지는 2020년 MLCC에 맞도록 블레이드를 개량했다. 삼성전기와 삼화콘덴서도 최근 엔티이엔지가 제작한 적층세라믹콘덴서(MLCC)용 초정밀 절단기를 검증하고 있다. 삼성전기는 현재 5차 테스트를 마치고 마지막 양산 테스트를 진행 중이다. 높은 정밀도가 요구되는 고용량 MLCC 제작에 엔티이엔지의 블레이드가 가장 적합하다는 판단에서다.
최초 개발 당시 미크론(㎛) 수준이었던 엔티이엔지의 초정밀 블레이드는 현재 나노미터(㎚) 단위로 훨씬 정교해졌다. 나노미터는 10억분의 1m를 가리키는 단위다. 1㎚는 성인 머리카락 굵기의 10만분의 1에 불과하다. 엔티이엔지가 개발한 블레이드는 500~800㎚ 수준이다. 조 대표는 “엔티이엔지의 블레이드는 국내 유일의 나노미터(㎚) 단위 정밀도를 갖춘 칼날로 평가받고 있다”고 강조했다.
엔티이엔지의 초정밀 블레이드는 텅스텐 계통의 초경합금으로 만들어진다. 조 대표는 엔티이엔지의 블레이드를 사용하면 전기차 배터리에 들어가는 양극재와 음극재도 훨씬 정교하게 절단할 수 있다고 주장한다. 그는 “양극재와 음극재의 버(burr·절단면의 상태) 사이즈를 3㎛ 이내로 자를 수 있다”고 설명했다.
최근 엔티이엔지를 방문한 일본의 가네마쯔 상사 관계자는 엔티이엔지의 블레이드에 대한 설명을 듣고 ‘최고의 칼’이라는 반응을 보이기도 했다. 조 대표는 “산업 전반에서 정교한 제품을 생산하려는 경향이 강해지고 있어 이를 제대로 절단할 수 있는 블레이드 수요가 늘어나는 추세”라며 “기존 장비 제작과 더불어 블레이드 제작 기술을 발판으로 세계적인 히든 챔피언으로 성장하는 것이 앞으로의 목표”라고 강조했다.
이정선 중기선임기자