전통 제조업체의 디지털 혁신
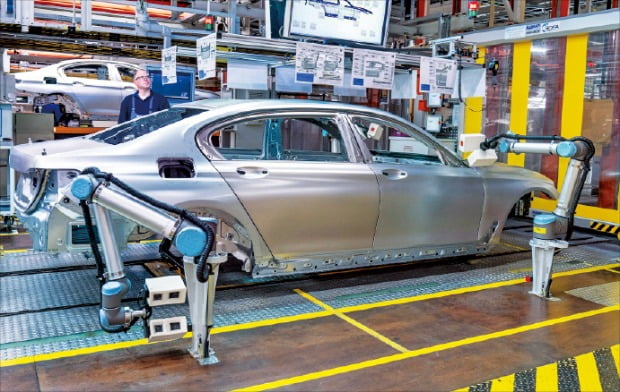
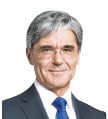
-조 케저 지멘스 회장, 2017년 ‘지멘스 이노베이션데이’에서
호주 서부에는 다른 곳에서 보기 어려운 기차가 있다. 많은 양의 광물을 광산에서 항구로 실어나르는 열차다. 운전석에는 아무도 타지 않는다. 세계 3대 광산업체인 리오틴토가 지난해 말 전면 도입한 자율주행 기차다. 운전자는 기차가 항구 인근에 오면 탑승한다. 평소엔 폐쇄회로TV(CCTV) 등으로 각 열차 상황만 파악할 뿐이다. 광물을 싣고 나르는 작업을 할 때도 사람이 필요없다.
리오틴토는 2014년 무인 열차의 시범운행을 시작한 데 이어 지난해 말 자율주행 기차를 전면 도입했다. 이 기차는 16개의 광산에서 채굴한 광물을 항구로 옮긴다. 인공지능(AI)이 열차의 동선이 꼬이지 않도록 조정해 병목현상을 줄였다. 운전자끼리 교대하는 시간도 사라졌다. 자율주행 기차 도입 후 광물의 운반 속도는 종전보다 5~6% 빨라졌다. 운반 비용은 15%가량 줄었다.
리오틴토는 트럭도 자율주행 트럭으로 교체하고 있다. 업계에서는 리오틴토가 지난해부터 2021년까지 자율주행 도입으로 4년간 50억달러(약 5조7000억원) 규모의 추가 이익을 거둘 수 있을 것이라는 관측이 나온다.
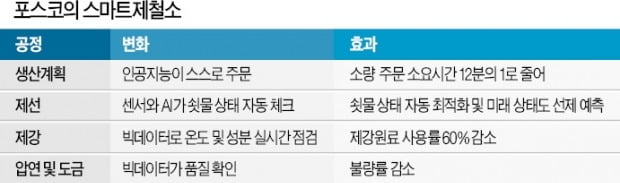
디지털 혁신과 거리가 멀 것 같던 전통 제조산업도 한 해가 다르게 바뀌고 있다. 대표적 노동집약산업으로 분류되는 광물업에도 사물인터넷(IoT), 빅데이터, AI, 머신러닝 같은 최첨단 기술이 도입되고 있다. 5년 전만 해도 제너럴일렉트릭(GE), 지멘스 등 일부 글로벌 기업만의 전유물로 여겨졌다. 이제는 대부분 제조업체가 디지털화를 추진하고 있다. 단순히 ‘시험삼아 해본다’는 수준이 아니다. 이미 성과도 나오고 있다. 전문가들은 “인력이 많이 필요한 제조업은 디지털 혁신으로 큰 성과를 낼 수 있다”며 “앞으로 디지털 혁신을 수용한 전통 제조업체만 살아남을 수 있을 것”이라고 조언했다.
자동차 제조공장의 모습도 바뀌고 있다. 독일 딩골핑에 있는 BMW 조립공장에서는 인간과 로봇이 함께 자동차 변속기를 생산하고 있다. 일부 공정을 로봇이 하는 수준이 아니다. BMW 직원이 기어 케이스를 놓으면 로봇팔이 5.4㎏에 달하는 기어를 들어올려 정확히 조립한다. 공장 다른 한쪽에서는 다른 로봇팔이 차량 창문 가장자리에 접착제를 바르고, 직원들은 접착제가 발린 곳에 창문을 끼운다.
생산공장에 로봇이 투입된 건 어제오늘 일이 아니지만 인간과 로봇은 각각 다른 공간에서 일해야 했다. 자칫 로봇 때문에 인간이 다칠 수 있어서다. 과거 로봇은 주변 환경을 인지하지 못해 정해진 움직임만 반복 수행했다. 하지만 센서와 AI 기술이 발달하면서 최근에는 인간과 로봇이 한 공간에서 일할 수 있게 됐다. BMW 공장의 로봇은 직원을 알아서 피해 부딪히거나 넘어뜨리는 일이 없다. 로봇과 인간의 협업을 통해 이 공장의 생산성은 기존 단독작업 때보다 85% 이상 개선됐다고 BMW는 설명했다.
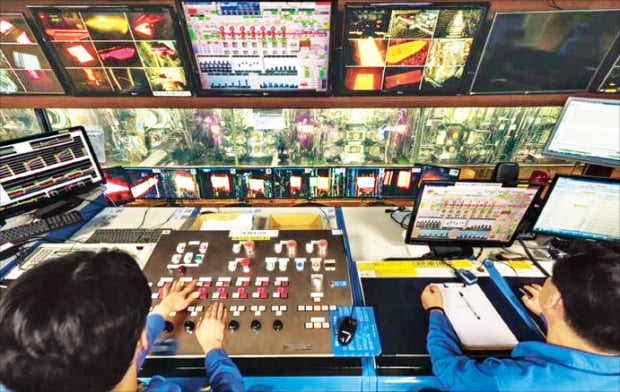
먼 나라의 일만이 아니다. 한국의 대표 철강업체인 포스코는 2015년부터 스마트제철소를 구축하는 작업을 시작했다. 생산계획부터 제선(철광석을 녹이는 작업), 제강(강철 덩어리를 제조하는 작업), 압연(강철 덩어리를 납작하게 해 담금질하는 작업) 등 모든 과정을 디지털화했다. 생산계획 단계에서는 AI가 빅데이터를 활용, 일부 제품에만 필요한 소량의 재료를 사전에 확보해 시간 낭비를 줄였다. 기존에는 제품 주문이 들어온 뒤에야 재료를 구매해 조달까지 12시간 정도 걸렸다.
제선 과정에서는 용광로 내부 상태를 스마트하게 확인할 수 있다. 과거에는 작업자가 2시간마다 쇳물의 온도를 점검하고, 철광석 샘플을 골라 상태를 확인해야 했다. 하지만 스마트제철소가 도입된 이후에는 AI가 고화질 영상을 보고 쇳물 및 철광석 상태를 점검한다. 다음날 용광로 상태를 예상해 최적의 환경이 되도록 조절할 수도 있다. 이 기술이 적용된 포항 2고로의 하루평균 생산량은 5340t에서 5580t으로 약 5%(240t) 증가했다. 이를 통해 연간 40억원의 비용을 절감했다는 게 포스코 측 설명이다. 포스코는 제강과 압연 등 다른 공정에도 AI, IoT, 빅데이터 등을 적용했다. 불량품을 걸러낼 때도 사람이 하나하나 점검하는 대신 AI가 맡는다. 이를 통해 비용과 검사시간이 대폭 줄었고, 불량률도 크게 낮아졌다.
권일명 AT커니 파트너는 “앞으로 1~2년 내 디지털 혁신을 이루지 않으면 전통 제조업체는 디지털을 기반으로 한 신흥 제조업체에 밀릴 것”이라고 지적했다.
도병욱 기자 dodo@hankyung.com