수직으로 쌓고, 수평으로 연결…반도체 기술 새 화두 '하나처럼 묶어라'
-
기사 스크랩
-
공유
-
댓글
-
클린뷰
-
프린트
Cover Story
한미반도체 '후공정 패키징' 강점
쏘잉·본딩 장비 등 글로벌 경쟁력
한미반도체 '후공정 패키징' 강점
쏘잉·본딩 장비 등 글로벌 경쟁력
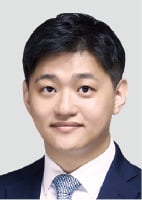
희망은 있다. 항상 패러다임의 변화는 기술의 절벽에서 나타나기 마련이다. 특히 2010년대 들어 미세 공정 지상주의의 반도체 업계를 흔드는 결정적인 기술 두 개가 상용화됐다.
첫째는 3D 적층 기술이다. 반도체에 소위 ‘이층집’을 만들기 시작했다. 2015년 D램을 4층으로 쌓아 올린 HBM(High bandwidth memory)이나 2017년 이미지센서, 시그널 프로세서와 메모리반도체를 3층으로 쌓아 올린 3단 적층 이미지센서가 좋은 예다. 이렇게 반도체를 수직으로 붙일 때는 두 반도체를 어떻게 연결하느냐가 핵심이다. 전통적으로 두 반도체를 연결할 때는 전선을 뽑아 붙이거나(리드프레임), 금속 공을 사이에 끼우는데(솔더볼), 이 방식들은 두껍고 속도가 너무 느려 하나의 반도체처럼 작동하지 않았다.
이를 극복하기 위해 삼성전자는 HBM이나 3단 적층 이미지센서에 TSV(Through Silicon Via) 기술을 사용하였다. 건물의 엘리베이터처럼 반도체들을 관통하는 구멍을 뚫는 방식이다. 인텔은 1층과 2층의 배선 부분을 솔더볼 없이 붙여 버리는 다이렉트 본딩 방식을 채용했고, TSMC는 가운데에 옥사이드층을 넣어 붙이는 하이브리드 본딩 방식을 도입하였다.
둘째는 칩렛(Chiplet)과 시스템 온 패키지(SOIP) 기술이다. 적층 기술이 세로로 쌓는 방식이라면 SOIP는 가로로 확장하는 기술이다. 반도체를 크게 만드는 것이 힘들다 보니, 일단 기능별로 잘게 쪼개어 만든 뒤 나중에 수평으로 이어 붙이자는 콘셉트다. 이때 기능별로 쪼갠 최소단위가 칩렛이다.
반도체 이어 붙이기에서 가장 중요한 것은 무엇으로 이음새를 연결할 것이냐이다. 반도체의 연결은 보통 반도체 기판을 이용하지만, 평범한 기판은 속도가 떨어져서 하나의 반도체처럼 작동한다고 볼 수 없다. 따라서 반도체와 같은 소재의 값비싼 실리콘으로 반도체를 연결한다. TSMC와 AMD는 바닥 면 전체를 실리콘으로 깔아(interposer) 해결했고, 인텔은 원가 절감을 위해 칩렛 사이에 실리콘 다리(silicon bridge)를 놓았다.
위 두 개의 차세대 패키지 기술을 융합한 것이 2.5D 패키지 기술이다. 즉, 메모리와 같은 몇몇 기능성 반도체는 적층으로 수직 연결하고, 기본적인 시스템은 칩렛 구조로 수평 연결하여 마치 하나의 반도체처럼 동작하게 만드는 패키지 기술이다. 홍콩 센트럴이나 여의도 IFC의 복합몰을 생각하면 편하다. 위로는 고층 빌딩들이 즐비하고, 아래로는 쇼핑몰로 모두가 연결되어 있어 마치 하나의 집 안을 돌아다니는 듯한 착각을 일으킨다는 개념이다.
결론적으로 미세 공정의 한계를 극복하기 위해 반도체 업체들이 꺼낸 카드는 후공정 패키지 기술들이다. 하나의 다이(Die)에 회로를 그릴 수 없다면 여러 다이를 하나처럼 붙이자는 아이디어는 단언컨대 혁신적인 변화다. 반도체 기술의 관점에서 2010년대까지는 얼마나 작은 회로를 그리느냐가 화두였다면 2020년대에는 얼마나 많은 반도체가 하나의 패키지로 연결되느냐로 변화할 것이다. 현재 나타나고 있는 반도체 고객사들의 투자에서 후공정 비중은 지속해서 늘어나고 있다. 후공정 장비 업체들의 기술 수준도 이제 맞춰 업그레이드되고 있다.
한미반도체는 후공정 패키징에 강점을 가진 회사이다. 패키지 쏘잉(package sawing) 장비와 본딩(bonding) 장비에서 글로벌 경쟁력을 갖추고 있으며 최근 마이크로쏘 내재화로 인한 추가 수익성 개선이 기대된다. 이오테크닉스는 레이저 그루빙(grooving)과 칩렛용 마커(marker), 그리고 패키지용 드릴 장비 등에서 수혜가 예상된다.
이종욱 삼성증권 연구원