'전기차 심장' 연 40만톤 쏟아진다…포스코 광양제철소의 변신
-
기사 스크랩
-
공유
-
댓글
-
클린뷰
-
프린트
포스코 광양제철소 '하이퍼 NO' 공장 최초 공개
전기차 모터 핵심 소재…"포스코 국내 유일 생산"
공장 준공 완료 시 총 40만톤 생산능력 확보
기가스틸 사업도 확장…"친환경차 소재 업체 도약"
전기차 모터 핵심 소재…"포스코 국내 유일 생산"
공장 준공 완료 시 총 40만톤 생산능력 확보
기가스틸 사업도 확장…"친환경차 소재 업체 도약"
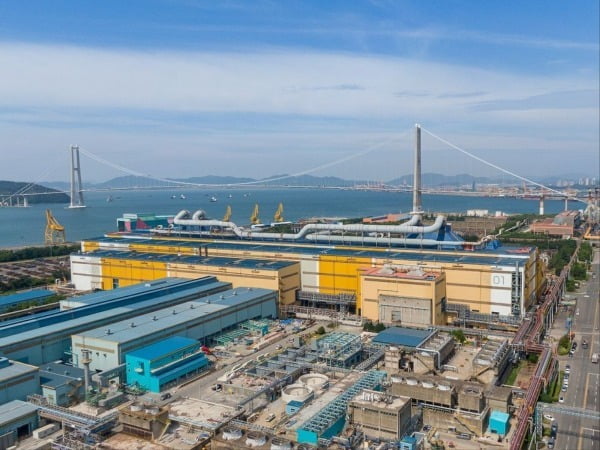
포스코는 내년 10월 2단계 준공을 완료해 추가로 연산 15만t 규모의 하이퍼 NO 생산능력을 확보할 계획이다. 이를 통해 연산 10만t 규모의 포항제철소에 이어 광양제철소에서 연산 30만t 규모로 제품을 생산할 계획이다. 총 40만t 규모로, 매년 전기차 500만대의 구동모터 코어를 만들 수 있는 양이다.
친환경차 모터 핵심 소재 '하이퍼 NO'
무방향 전기강판은 전기차를 비롯한 친환경차의 심장인 모터의 핵심 소재다. 전기강판은 규소를 1~5%에 함유해 일반 강판 대비 전자기 특성이 뛰어나고 철손(모터코아의 철심에서 발생하는 전력손실)이 낮다. 전기강판은 방향에 따라 활용 범위가 달라지는데, 모든 방향에서 균일한 자기적 특성을 보이는 무방향 전기강판은 모터에 탑재되는 로터와 스테이트를 만드는 데 쓰인다. 무방향 전기강판은 철손값에 따라 등급이 나뉘는데, 하이퍼 NO는 철손값이 3.5W/㎏(1㎏당 3.5와트) 이하인 고효율 제품이다.하이퍼 NO는 글로벌 완성차 업체들의 전동화 추세에 맞춰 수요가 급격하게 증가하고 있다. 전력손실이 적은 전기강판일수록 모터 회전속도가 빨라져 전기차의 주행거리를 늘릴 수 있기 때문이다. 포스코는 지난해 4월 1조원을 투자해 광양제철소의 무방향성 전기강판 공장 착공에 나선 배경이다.
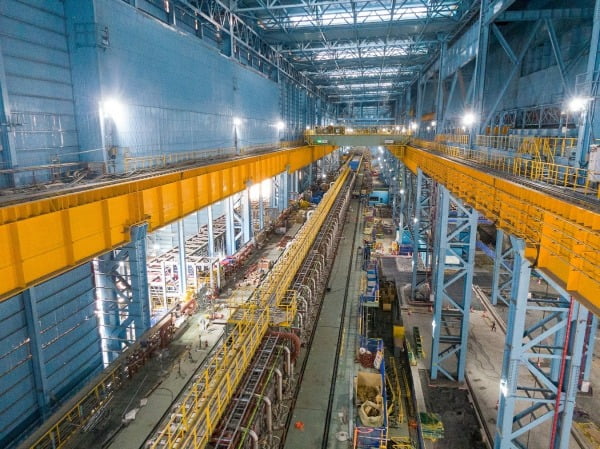
포스코는 하이퍼 NO를 소둔산세공정(APL)과 압연공정, 소둔코팅공정(ACL) 등 세 공정을 통해 생산한다. 제강과 열연을 거쳐 생산된 열연코일은 APL 공정을 거쳐 하이퍼 NO의 기본 모습으로 만들어진다. APL은 열 연판을 1200도의 고온에서 열처리해 제품 균일성을 확보하고, 열연코일 표면에 잔류한 산화층을 제거하는 설비다. 이후 압연기인 ZRM 설비를 거쳐 길이 방향과 폭 방향의 균일한 두께 품질을 확보하게 된다. 이런 과정을 거친 후 ACL 설비를 통해 최종제품 생산이 이뤄진다.
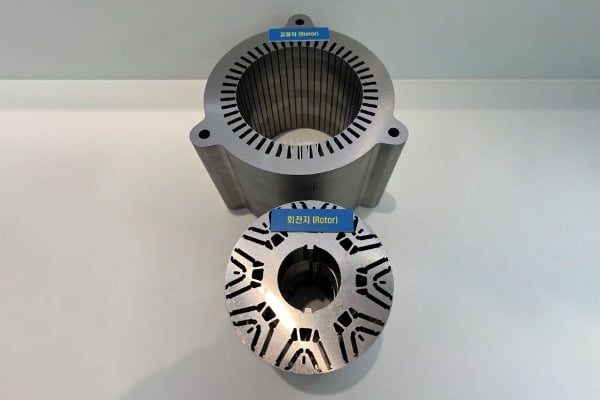
'기가스틸' 거점 확보에도 주력 "친환경 소재 전문업체 도약"
포스코는 꿈의 강판이라 불리는 초고강도 강판 ‘기가스틸’에도 속도를 낸다. 1제곱밀리미터 면적당 100kg 이상 하중을 견딜 수 있어 차량 부품 소재 두께를 줄여 경량화가 가능하다. 전기차는 배터리팩의 무게로 내연기관 차량보다 무게가 25%가량 더 무겁기 때문에 안정적이면서도 가벼운 무게를 갖춘 기가스틸 수요가 늘어나는 추세다.포스코는 일찌감치 기가스틸 고도화에 뛰어들었다. 기가스틸을 45% 이상 적용해 기존 차체 대비 차량 무게를 26%가량 줄인 전기차 차체 실증 모델을 최초로 개발했다. 2021년 9월엔 기가스틸 100만t 생산체제를 구축하고, 중국 현지 가공센터인 ‘포스코-CSPC’에 기가스틸 전문 복합가공 공장을 준공했다. 현재 건설 중인 연산 90만t 규모의 자동차용 도금강판 공장에도 기가스틸 생산 라인을 구축할 예정이다.
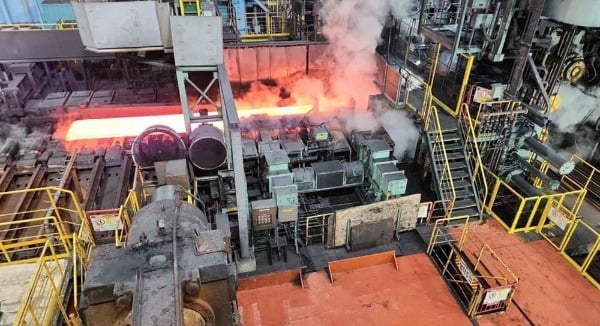
광양=배성수 기자 baebae@hankyung.com