미래 모빌리티 시대, 車부품 '모듈·슬림화'로 정면 돌파 [산업리포트]
입력
수정
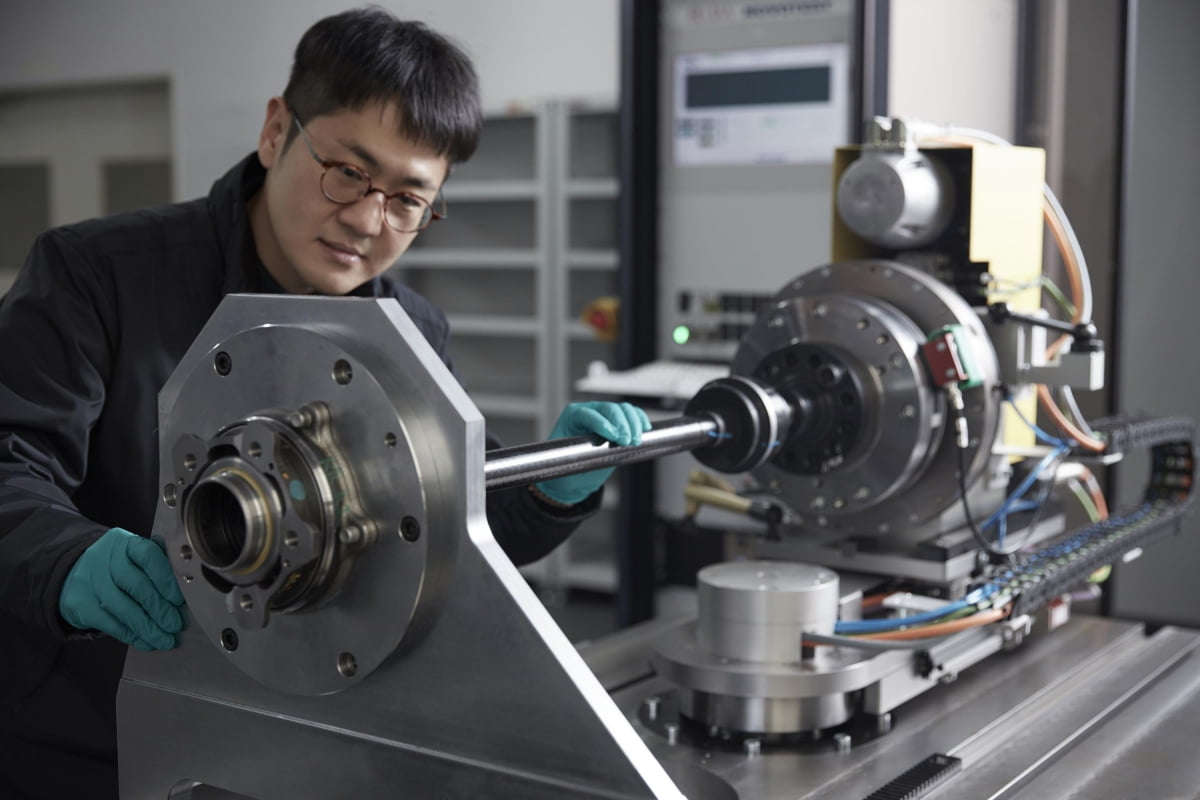
등속조인트의 기본 구조는 1920년대 내연기관이 처음 개발된 후 크게 바뀌지 않았다. 부품이 노후화 되면 힘을 받는 주요 연결 부위가 파손되는 문제가 있었다. 더욱이 배터리 무게 등으로 차체가 무거워지고, 전기가 흐르면 바로 전속력으로 가속이 가능한 전기차 시대에는 동력을 전달하는 연결 부위의 강성이 더욱 중요해졌다.
이에 지난해 현대위아는 등속조인트와 휠베어링 등 인접 부품을 하나로 합친 ‘기능통합형 드라이브 액슬(IDA)’을 개발하고 관련 특허를 국내외에 출원했다. 연결 부위를 일체화 해 기존 구조 대비 강성을 55% 가량 높였다는 게 현대위아의 설명이다. 부품 크기도 작아져 차체가 평평한 전기차에도 장착할 수 있게 됐다. IDA는 현대자동차 고성능 전기차 아이오닉5N 등에 적용됐다.
◆“기능 통합하며 모듈·슬림화”
자동차업계에 따르면 미래 모빌리티 시대를 준비하기 위해 현대차그룹 주요 계열사가 부품 ‘모듈화’와 ‘슬림화’에 나서고 있다. 기계식으로 유사한 기능을 하는 부품은 전자식으로 대체해 통합하는 방식 등이 주로 활용된다. 덕분에 부품 구조는 간단해지고 무게는 가벼워진다. 또 과거에는 엔진 등 핵심 구동장치에 밀려 주목받지 못했던 분야인 열관리·시트·내비게이션 관련 기술 확보에도 주력하는 모습도 보였다.현대위아는 지난해 전기차 전용 열관리 시스템 ‘냉각수 허브 모듈’을 개발하고 경남 창원 공장에서 본격 생산에 들어갔다. 연간 21만개 분량이다. 해당 부품은 기아의 대형 전기 스포츠유틸리티차량(SUV) EV9과 현대차 신형 코나 일렉트릭 등에 탑재된다.
냉각수 허브 모듈은 배터리와 모터 등 구동장치 및 전장(전기전자장비) 부품의 열을 동시에 효율적으로 관리할 수 있는 부품이다. 냉각수 탱크와 워터펌프, 밸브 등의 기능을 통합했다. 배터리의 온도를 최적의 상태로 유지하며 구동장치에서 발생하는 열도 관리한다. 현대위아 관계자는 “전기차에 최적화한 모듈로 관련 부품 수를 크게 줄였고 모터룸의 공간 활용도 역시 극대화할 수 있었다”고 설명했다.
◆필요부품 3만→1만8900개
한국자동차연구원에 따르면 자동차 산업이 100% 전동화될 경우 필요 부품 수는 1만8900여개로 줄어든다. 기존 내연기관차(3만개) 대비 37% 감소한다. 동력을 전달하는 구동계 부품은 5700개에서 3600개로 줄어든다. 전장부품 역시 차량용 반도체 등이 고도화됨에 따라 3000개에서 900개로 감소한다. 엔진을 구성하는 6900개의 부품은 모두 사라진다.이에 현대모비스 역시 최근 △로어암 일체형 판스프링 △저상형 드라이브 모듈 △기능 통합형 전동액슬 등의 부품 개발을 완료했다. 현대모비스 관계자는 “미래 모빌리티 시대에는 핵심 분야의 모듈화된 코어 부품 기술을 확보하는 것이 더욱 중요해졌다”고 설명했다.
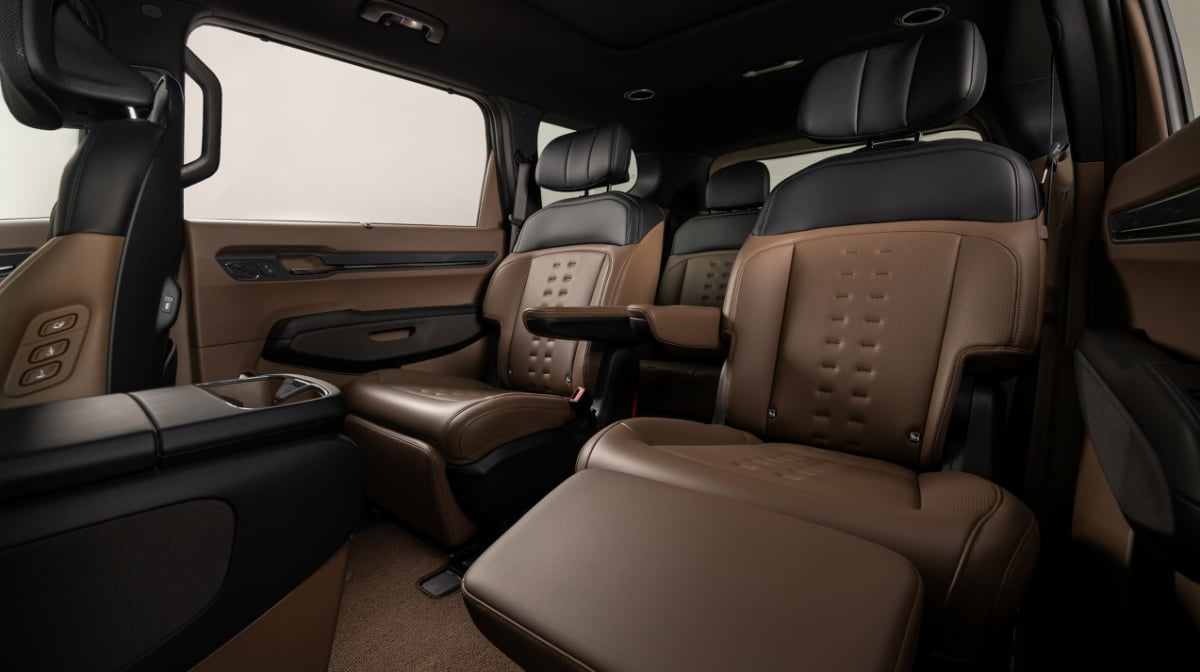
현대차·기아에 장착되는 순정 내비게이션용 SW를 개발하는 현대오토에버는 지난해 △항공 촬영 영상을 이용한 고정밀(HD) 지도 정보 구축 △차량 무선 업데이트 관리 제어 방법 및 장치 등의 기술을 개발했다. 모두 완전자율주행(레벨4) 등 미래 모빌리티를 개발하기 위한 핵심 기술이다. 자율주행은 먼저 차량의 위치를 정밀하게 확인하는 것에서 시작한다. 카메라·센서 등으로 주변을 추가로 인식한 뒤 도로 상황 및 주행 코스에 맞게 차량을 제어하는 순서로 이뤄진다.
현대오토에버는 현재 내비게이션에 사용되는 오차범위 1m 안팎의 도로망 정보 표준지도(SD)를 업그레이드하고 있다. 10㎝ 오차 범위를 갖는 고정밀(HD) 지도 기반 내비게이션을 개발 중이다. 이후 차량 간 통신 등의 기능을 구현하면 완전자율주행의 첫 단추를 끼울 수 있다는 것이 현대오토에버의 설명이다.
김진원 기자 jin1@hankyung.com