日 아사히글라스는 어떻게 화학 산업에서 디지털 트윈을 선도했나
입력
수정
지면B5
기고 / 윤정호 시마크로 대표
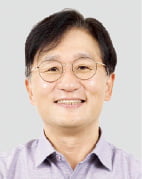
작년부터 성과가 나오기 시작했다. ‘공정 디지털 트윈’이다. 1월과 4월 각각 유리 용해 공정과 염화비닐 제조 공정에 대한 디지털 트윈 시스템 구축 성과를 발표했다.디지털 트윈은 점점 치열해지는 글로벌 화학업계에서 경쟁력을 확보하기 위한 필수 선택이다. 코로나 팬데믹 이후 중국 기업들이 설비를 대폭 늘리며 단가 경쟁을 시작했다. 기존 기업들은 체질 개선이 시급한 상황이다.
지난해 국내 산업계의 경우, 총 수출량은 증가했지만 단가 하락으로 수출액은 전년과 비슷한 수준에 그쳤다.
AGC가 갖고 있던 고민도 이런 맥락에서 출발했다. 우리(시마크로)는 공정 디지털 트윈을 통해 이들이 더 나은 의사 결정을 할 수 있도록 도움을 줘야 했다. 더 낮은 단가와 더 높은 생산성을 위한 제안이다. 아무도 해 본 적 없는 작업이라 문제를 정의하는 일부터 시작했다. AGC와 시마크로가 가장 고민한 부분이었다.화학 열분해 설비는 많은 에너지가 필요하다. 천연가스 및 수소 등 혼합 연료 사용에 따른 높은 운전 비용과 환경 영향 등을 고려해 에너지 최적화를 해야 한다.
공정 디지털 트윈을 이용하면 가장 적은 비용으로 최고 효율을 낼 방법을 빠르게 찾을 수 있다. 시마크로의 디지털 트윈으로 플랜트 내 화구 위치를 조정하고 가상 운전을 진행하니, 더 적은 화력으로 동일한 공정을 운영할 수 있다는 결과가 나왔다.
AGC는 분석 결과를 믿고 과감히 실제 설비를 조정해 테스트했다. 디지털 트윈의 결과가 그대로 구현됐고, 이를 바탕으로 공정을 수정했다. 이어 디지털 트윈 시스템 유지·보수와 고도화를 우리에게 의뢰했다. AGC 프로젝트는 세계적으로 전례를 찾기 어렵다. 화학 분야에서 혁신적인 디지털 전환 사례라고 할 수 있다.공정에 존재하는 문제를 파악하고 해결책을 찾으려면 다각도로 접근해야 한다.
AGC 공정 디지털 트윈을 구축할 때 총 다섯 가지 소프트웨어를 활용했다. 설비가 가진 물리적 특성을 가상으로 구현하고, 공정에서 일어나는 원료의 화학적 변화를 이론적으로 계산하고, 실시간으로 발생하는 센서값을 데이터로 변환해 축적하고, 이를 활용해 시뮬레이션을 진행하고 그래프로 시각화해 보여주는 모든 과정에 각각 다른 소프트웨어가 필요하다.
공정 디지털 트윈을 위한 새로운 도구가 필요한 상황이다. 공정 디지털 트윈을 다양한 기업에서 손쉽게 도입할 수 있는 ‘만능’ 솔루션을 개발하면 전 세계에서 주목하겠다고 생각했다.
설비에서 발생하는 데이터를 원하는 기준에 따라 배열하고, 시각화하고, 레시피를 변경했을 때 결과가 어떤 영향을 받는지 예측하고, 최종적으로 인공지능(AI)의 도움을 받아 공정 최적화를 위한 조언까지 받을 수 있도록 소프트웨어를 개발하고 있는 이유다.